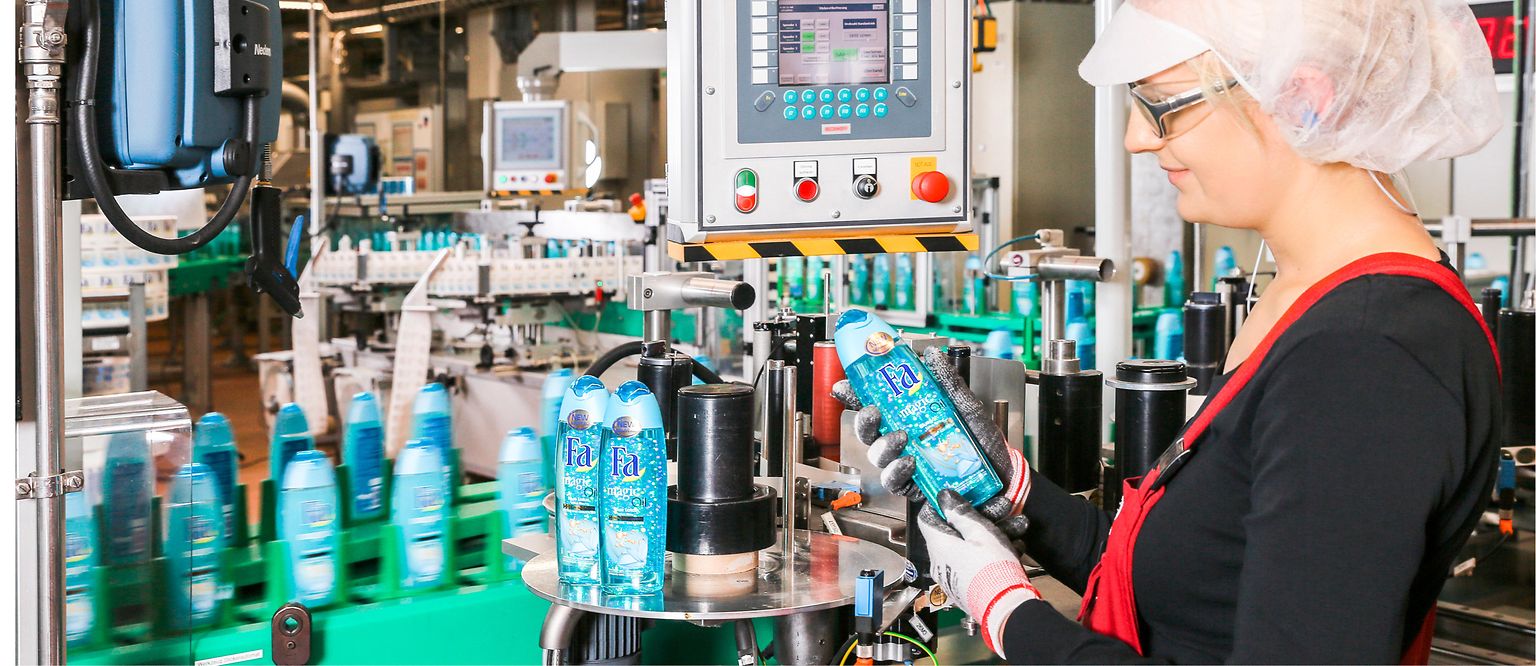
Never stop optimizing your production
The analysis software for automated production lines and machines based on high-frequency machine data. Adapted to your production - as Software as a Service.
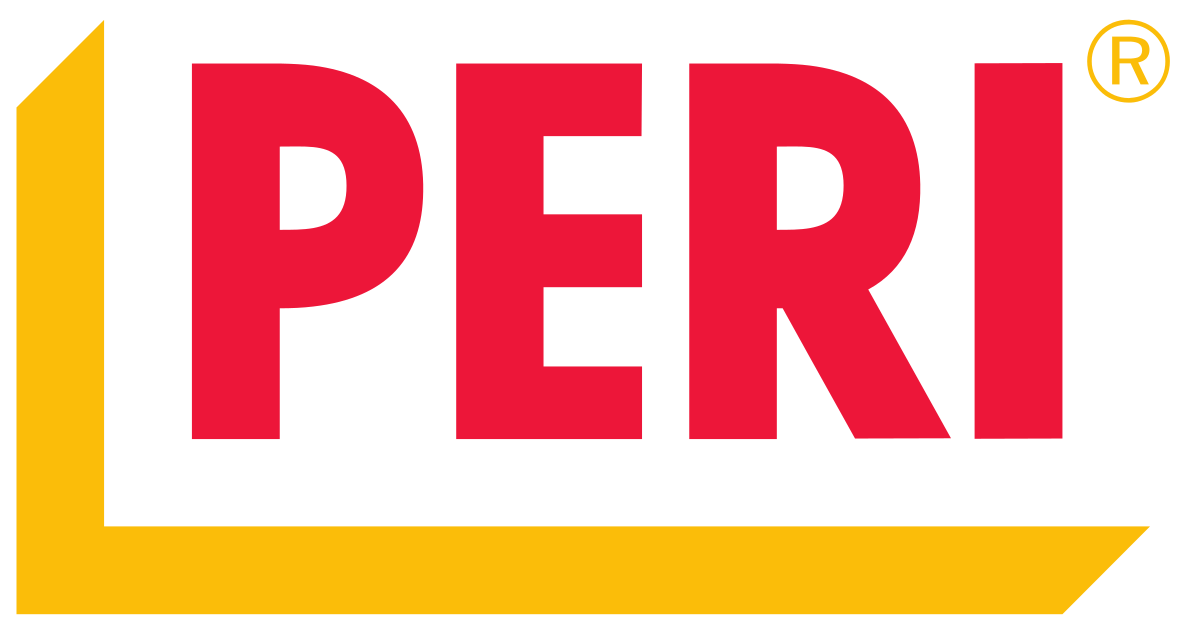
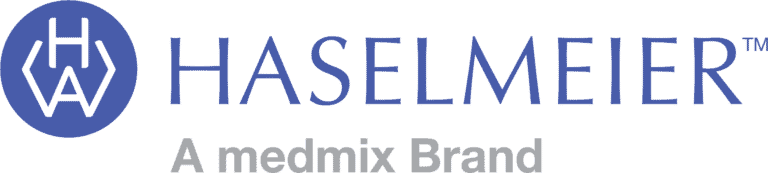


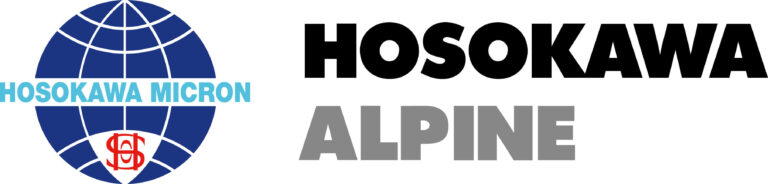
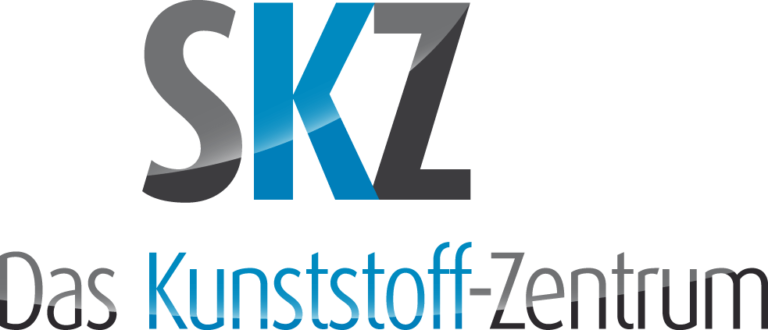
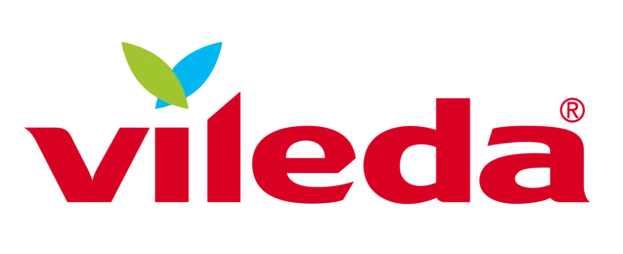
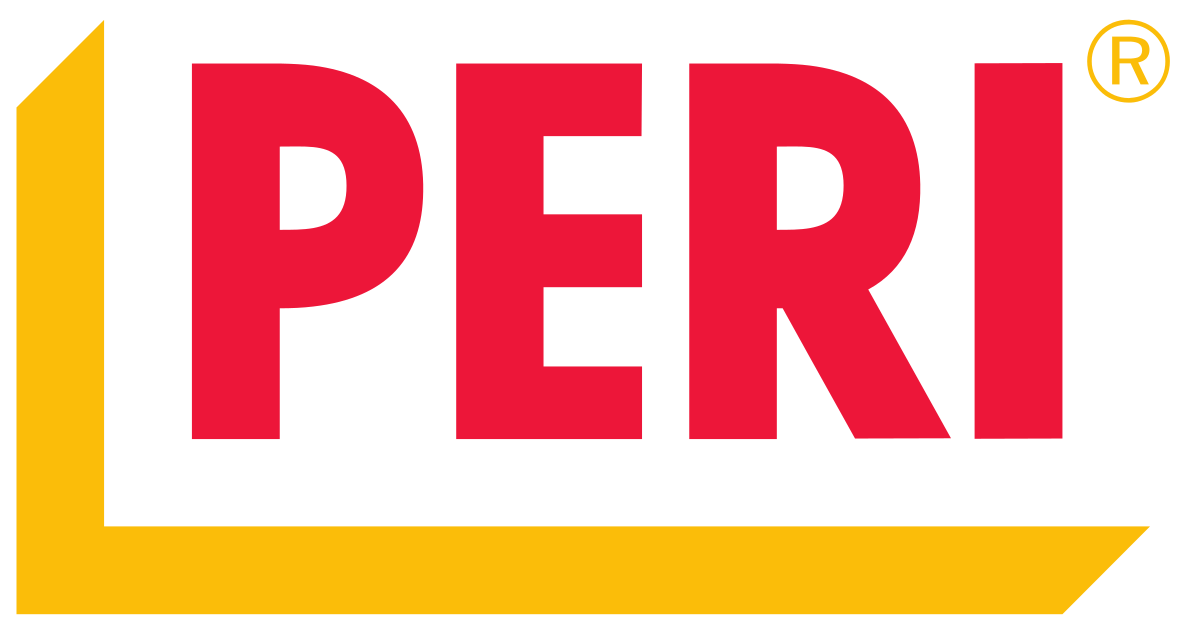
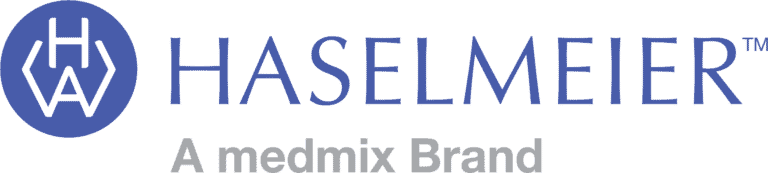


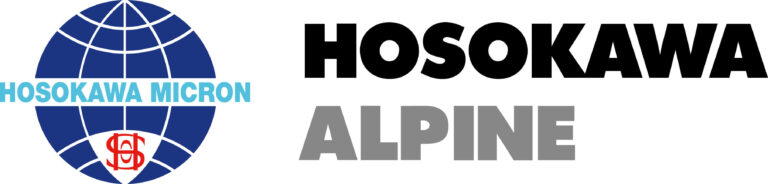
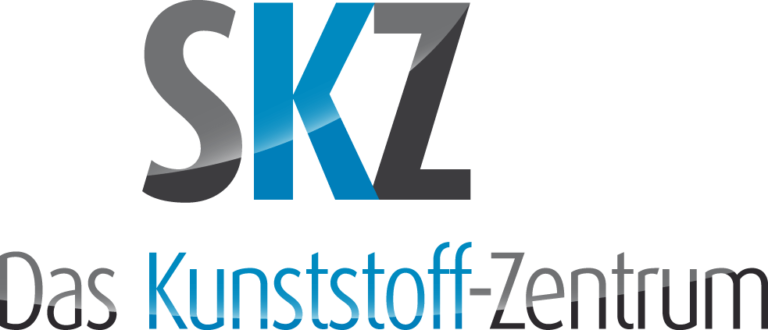
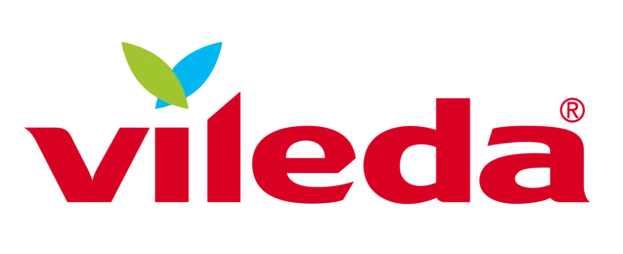
Continuous productivity optimization of highly automated production lines and machines
plus10 Analytics software identifies problems and optimization potential based on high-frequency machine data
Complex manufacturing processes often have too low OEE
Identifying the causes of productivity losses in automated production lines and machines is often difficult. Complex interdependencies, many process dependencies and a lack of expert knowledge make problem analyses difficult.
plus10 software creates transparency about OEE losses in order to turn the right screws.
"Shannon has already brought us about 5% more productivity during the pilot phase."
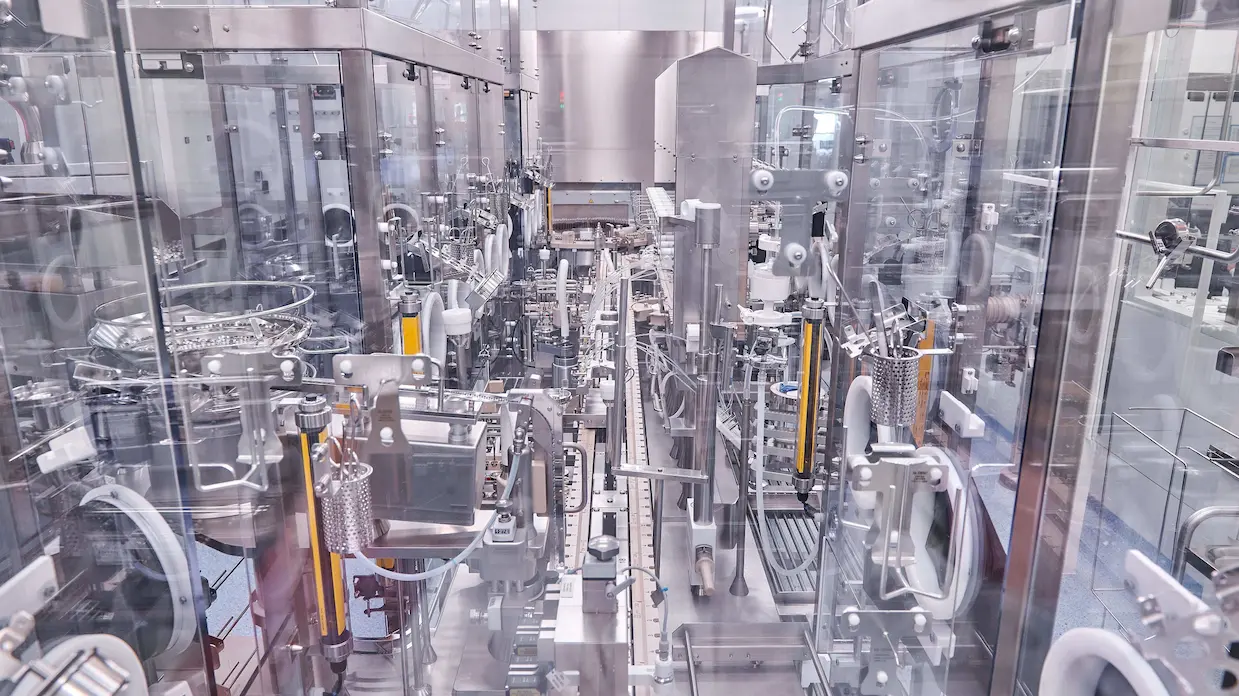
Lack of personnel is increasingly the cause of production losses
The shortage of skilled workers is often already omnipresent. Missed production shifts and reduced technical availability are the result.
Turn your shop floor staff into experts with Shannon® , enabling more machine operation and reduced downtime due to a reduced MTTR.
"The smartwatches for operational operators and logistics personnel were particularly valuable here."
_IMB.webp)
Fluctuating material quality and environmental parameters cause unstable processes
Variable material parameters, such as those that occur when using recycled material, can lead to increased scrap. A situational adjustment of the setting parameters of the injection molding process is required.
Use Hopper to continuously receive suggestions for adjusting set parameters in order to reduce scrap and cycle time.
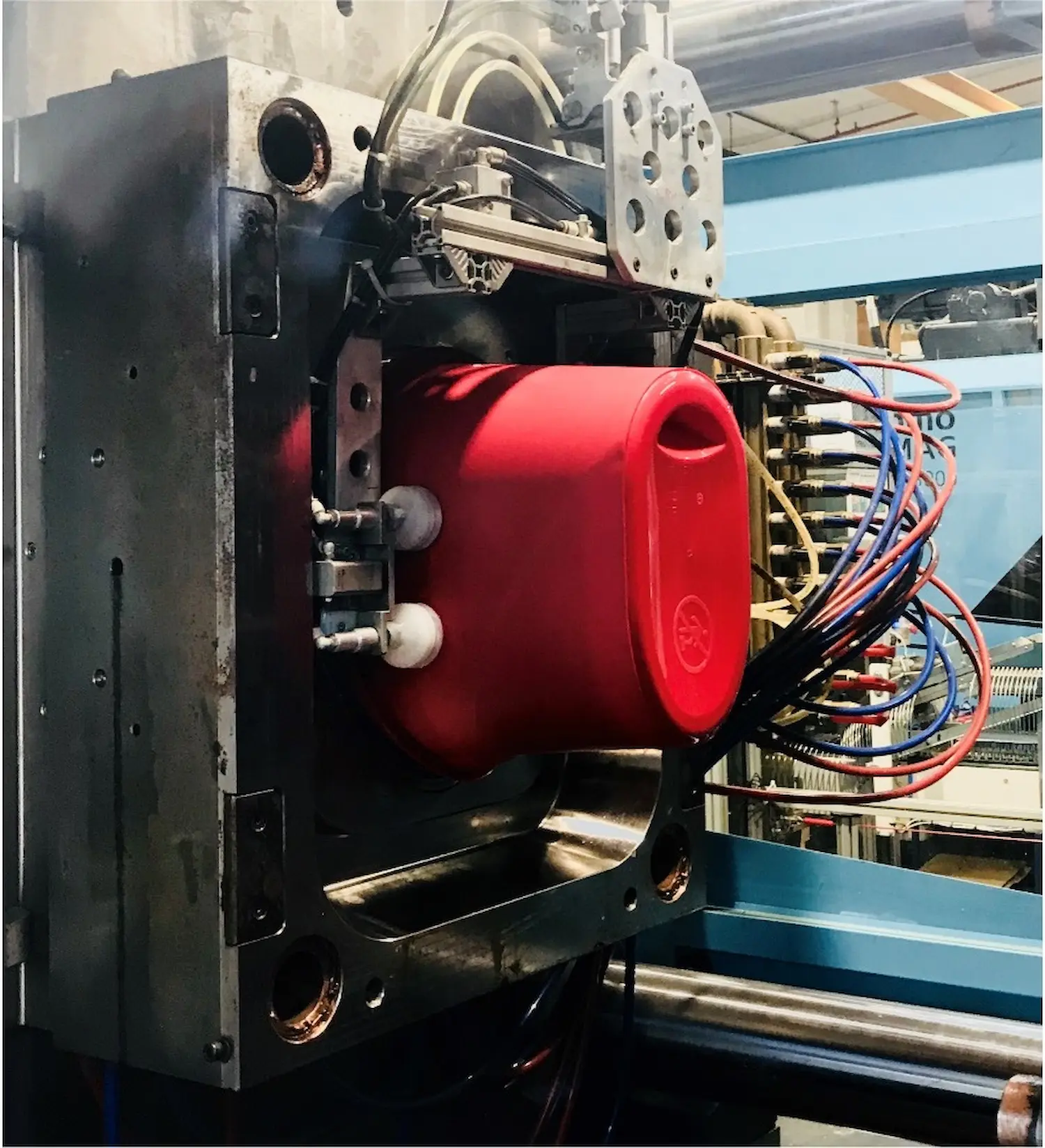
The ramp-up of production lines and machines often takes far too long
Complex interactions in automated production lines and machines are often the cause of long ramp-up phases with too low OEE.
Analyze manufacturing processes in detail with Darwin to clearly identify performance losses.
Create a knowledge base for troubleshooting with Shannon® right from the start.
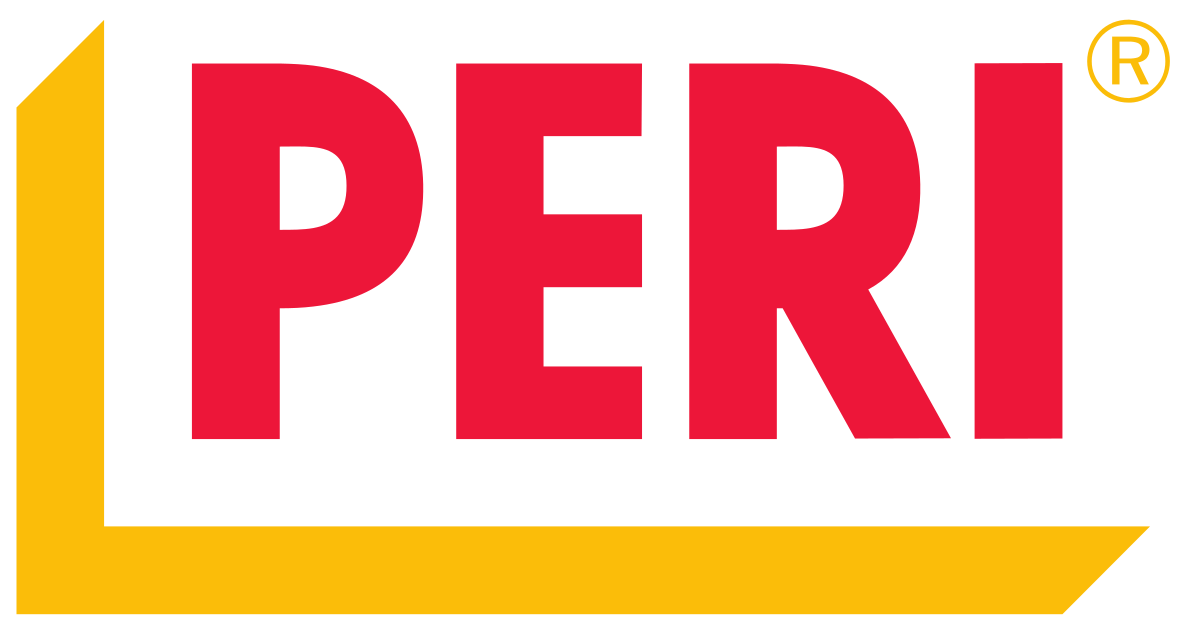
"We were able to generate data-based visibility into all relevant machine faults, including localization and prioritization."
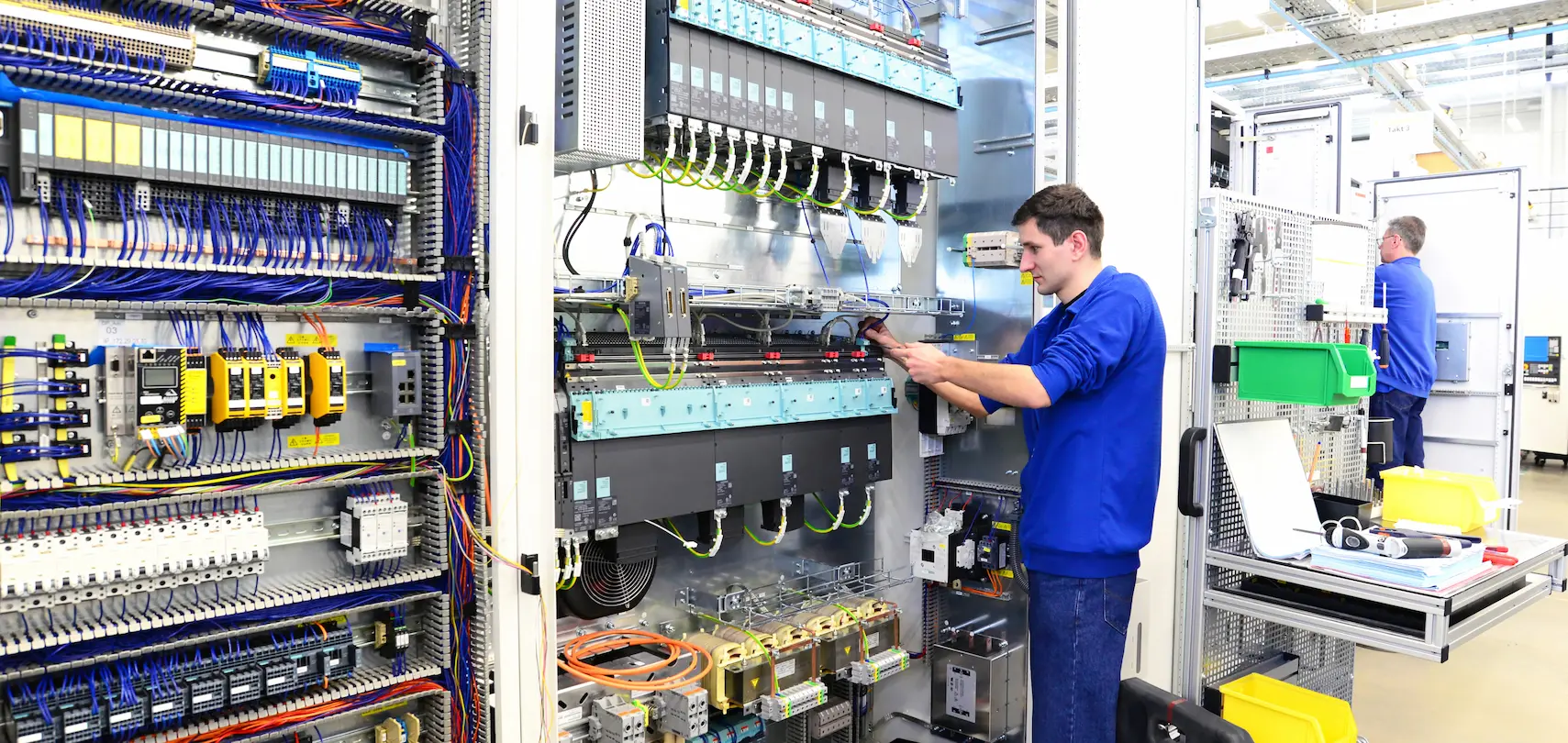
We accompany you in the following industries
Our software solutions are adapted to your industry specifics and can thus generate concrete added value in your industry.
Industry not included?
We customize our software solution to your problem. Talk to us!
Intelligent software that identifies problems and suggests solutions
Our analysis software addresses the three OEE loss categories of technical availability, performance level and quality
What our customers & partners say
Request a free use case evaluation now.
- Product presentation with demo
- Roadmap for problem solving
- Holistic evaluation of the approach
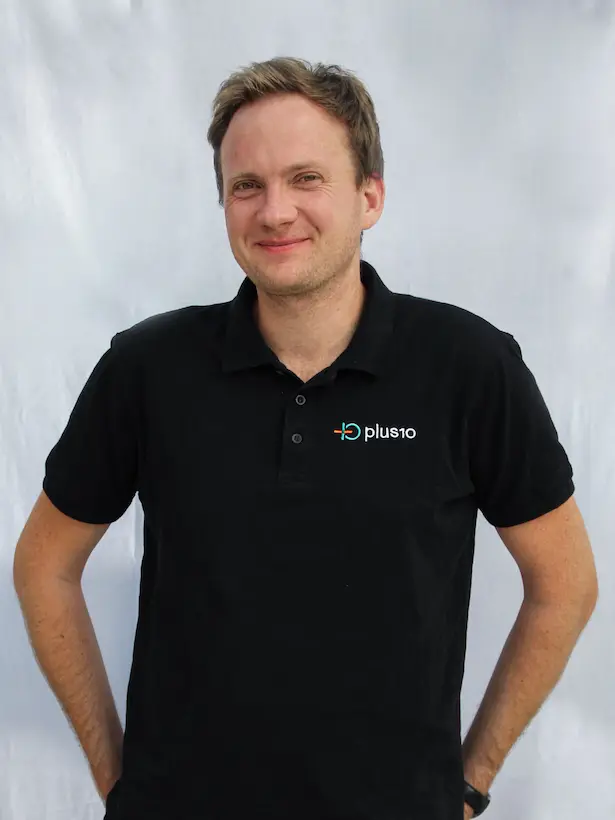
News from plus10.
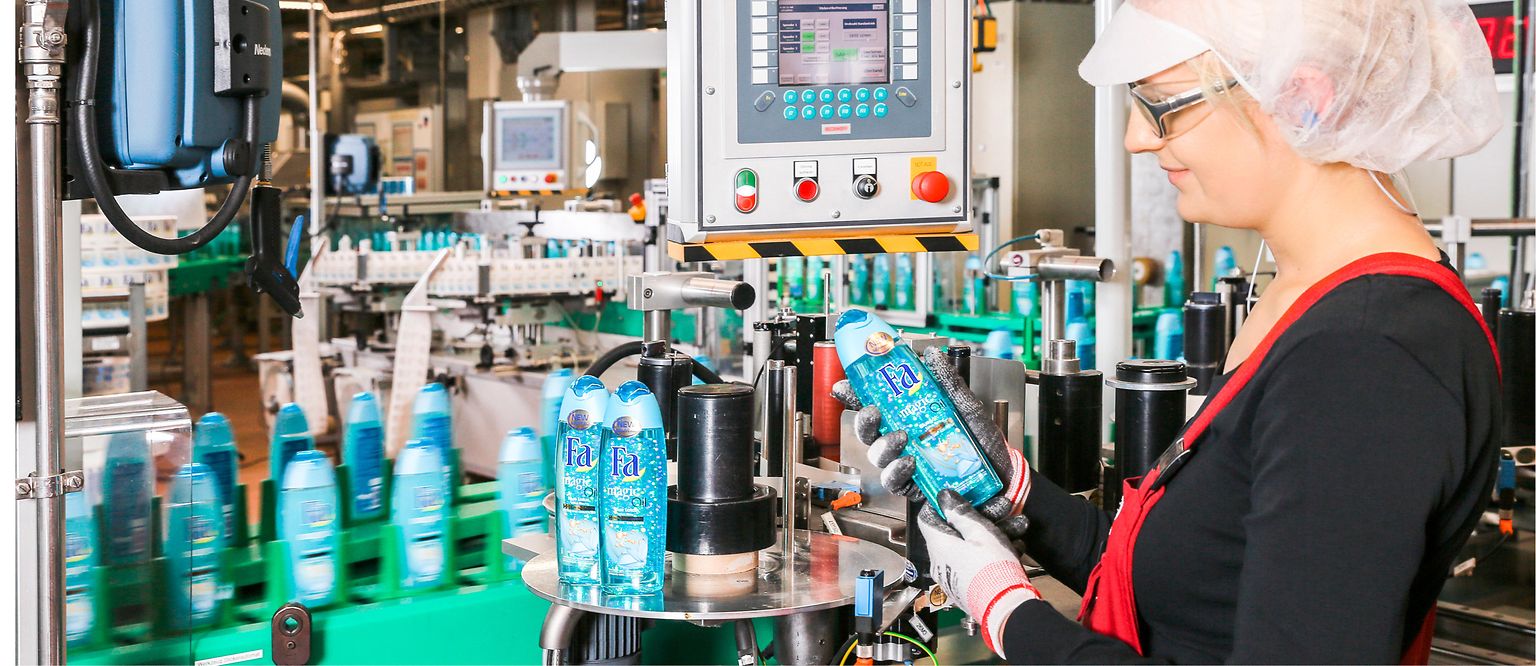
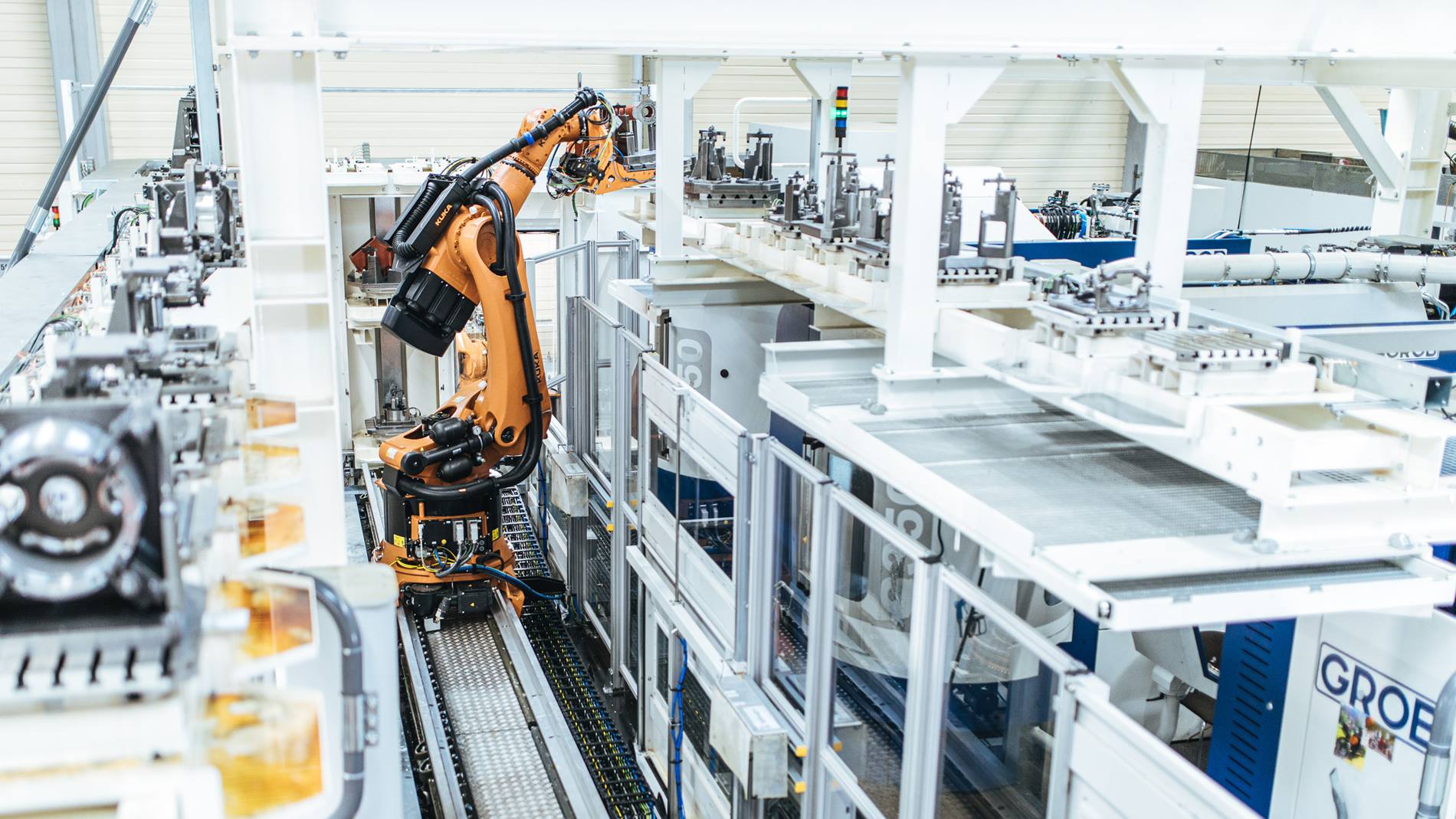
Cycle Time Optimization in Automated Machining
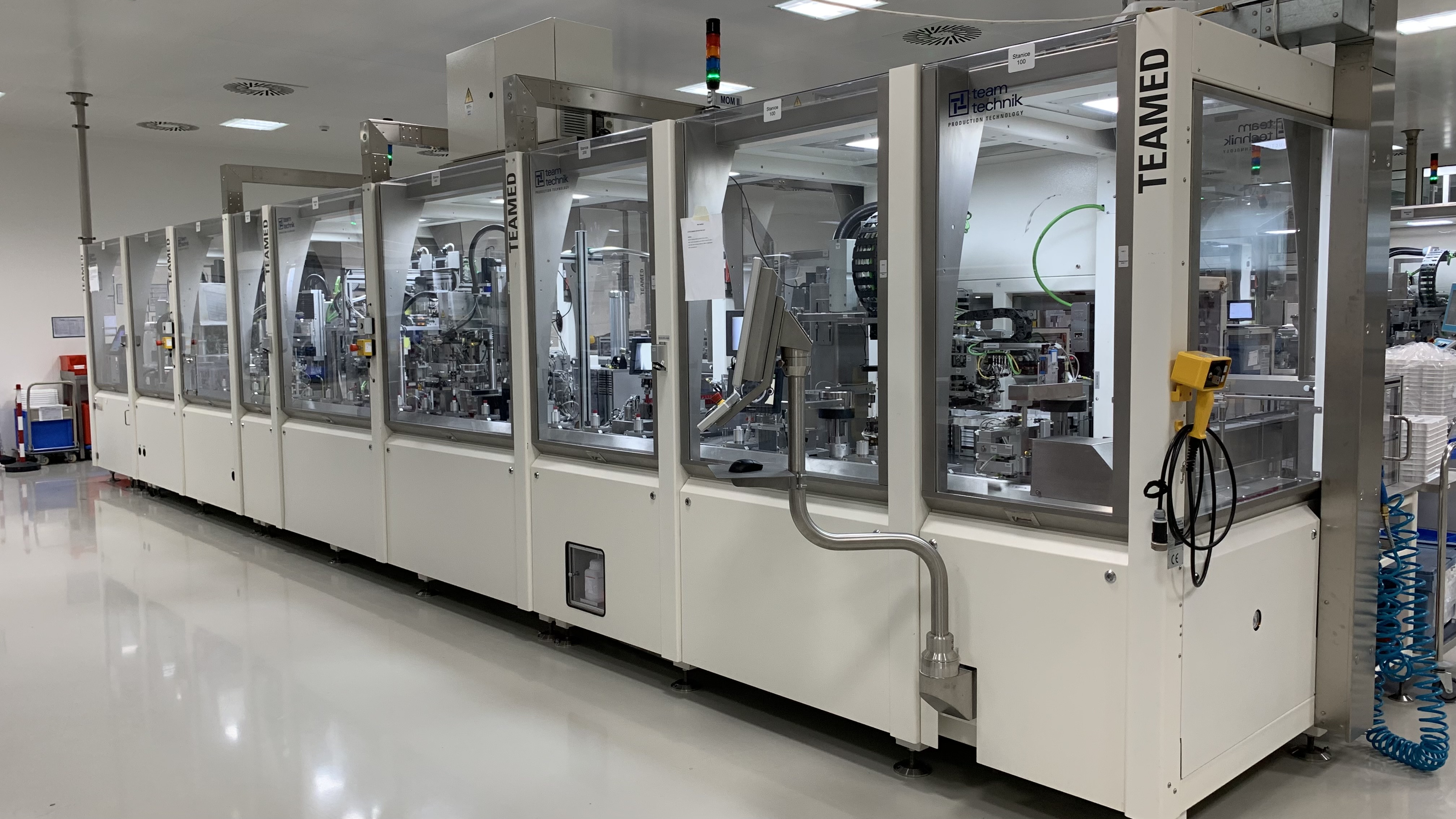