Success stories in the pharma and medtech sector
Optimize your manufacturing with continuously learning and situationally acting software
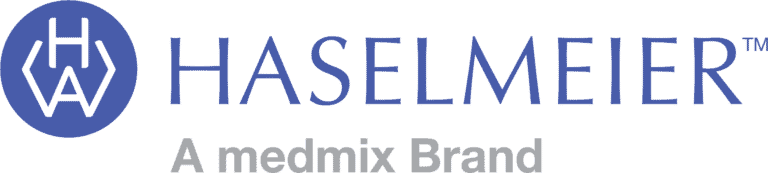
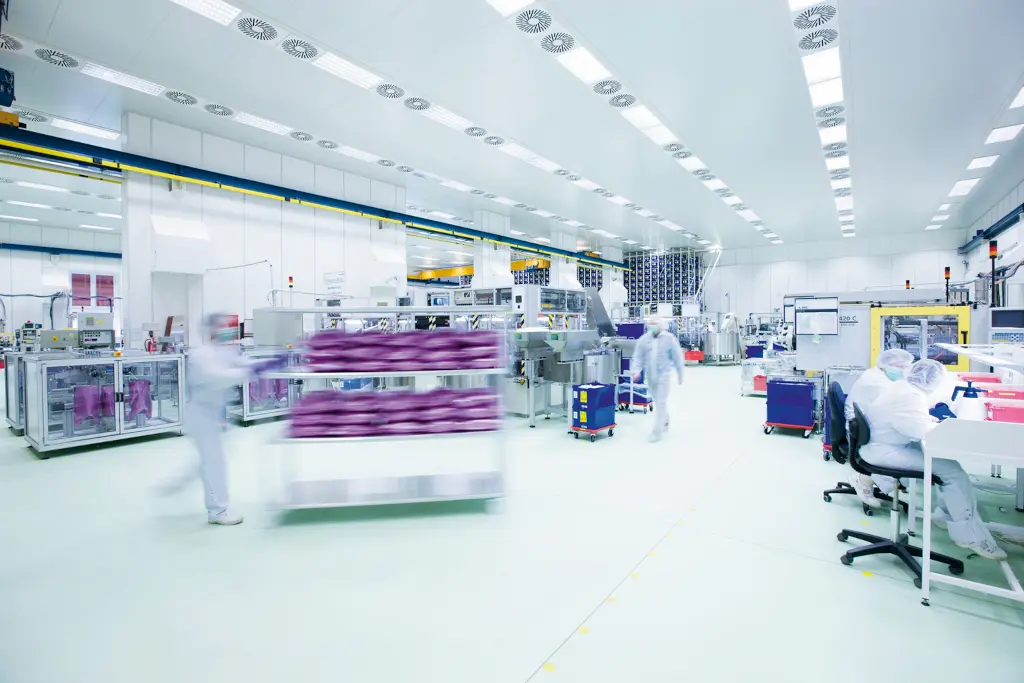
Offer digital software tools to your customers to increase your production lines and machines productivity
plus10 Analytics software identifies problems and optimization potential based on high-frequency machine data. With integration into your plants, you offer real added value.
Operating complex production lines and machines efficiently is a challenge
In addition to product modularization and standardization, digital innovations play an important role in their product portfolio. End customers are demanding, for example, digital services and digitally enhanced machines, which
- Make complex support requests easier and more transparent to resolve
- Optimize operating efficiency and
- guarantee the availability of the machines through data-driven technologies.
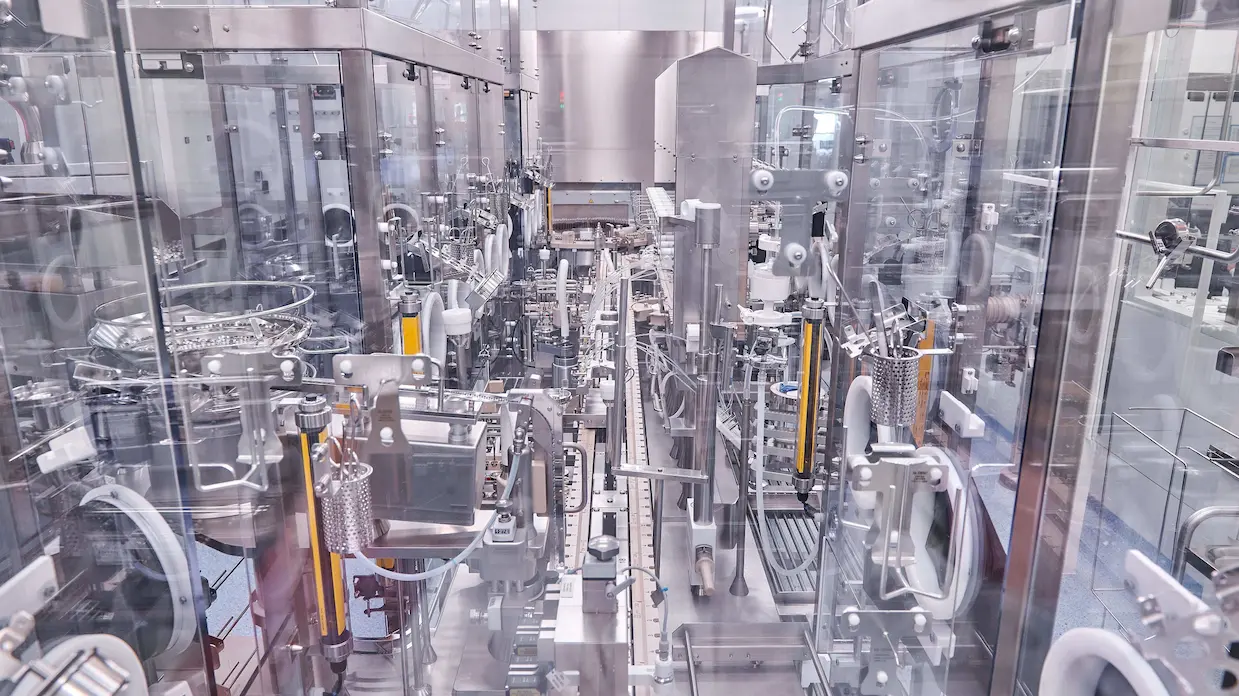
Optimization of production lines and machines as a digital service
Integrate plus10 software products into your production lines and machines and offer your customers added value in the efficient operation of your machines and production lines.
- Shannon provides custom-fit suggestions for troubleshooting even the most complicated issues
- Darwin creates transparency about machine behavior: So you understand what happened - even remotely
- Optimization of bottlenecks and faults during commissioning
_IMB.webp)
What our customers & partners say
Advantages in the pharmaceutical and medical technology sector
5-15%
Increase OEE by reducing downtime (MTTR)
Up to 38%
Reduction of the average productivity variation
10 - 30%
Shortening the start-up and relocation phase
Software solutions - made for your industry
- Our optimization tools are designed to meet GMP (Good Manufacturing Practice) standards. In doing so, we take into account the risk-based approach of EU GMP Annex 11, the practical GAMP 5 guide, and the Computerized System Validation (CSV) procedures.
- Generated suggestions and measures are documented in a GMP/FDA-compliant manner
- Auditing of changes and important events
- Optional approval process when adding new disruption measures in the system (dual control principle)
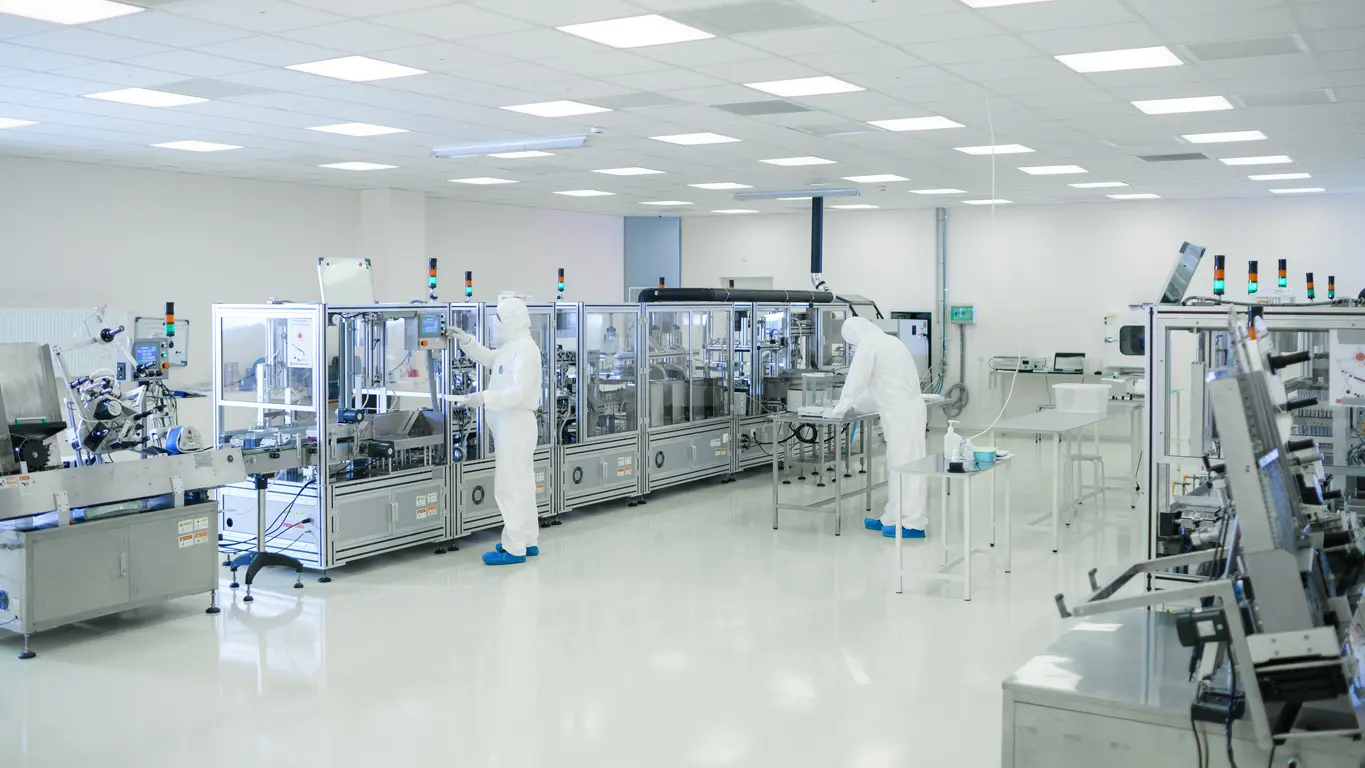
With our products to success in mechanical and plant engineering
Our analysis software addresses the three OEE loss categories of technical availability, performance level and quality.
Darwin - Identifying causes of performance losses
- Uncover bottlenecks in your production lines and machines and create transparency about the causes of performance losses - down to the signal level.
- Increase output rate per machine by reducing cycle time
- Explanation of why similar machines in the same factory work differently
- Detect trends in malfunction and process time data at an early stage and thus implement optimizations in a timely manner
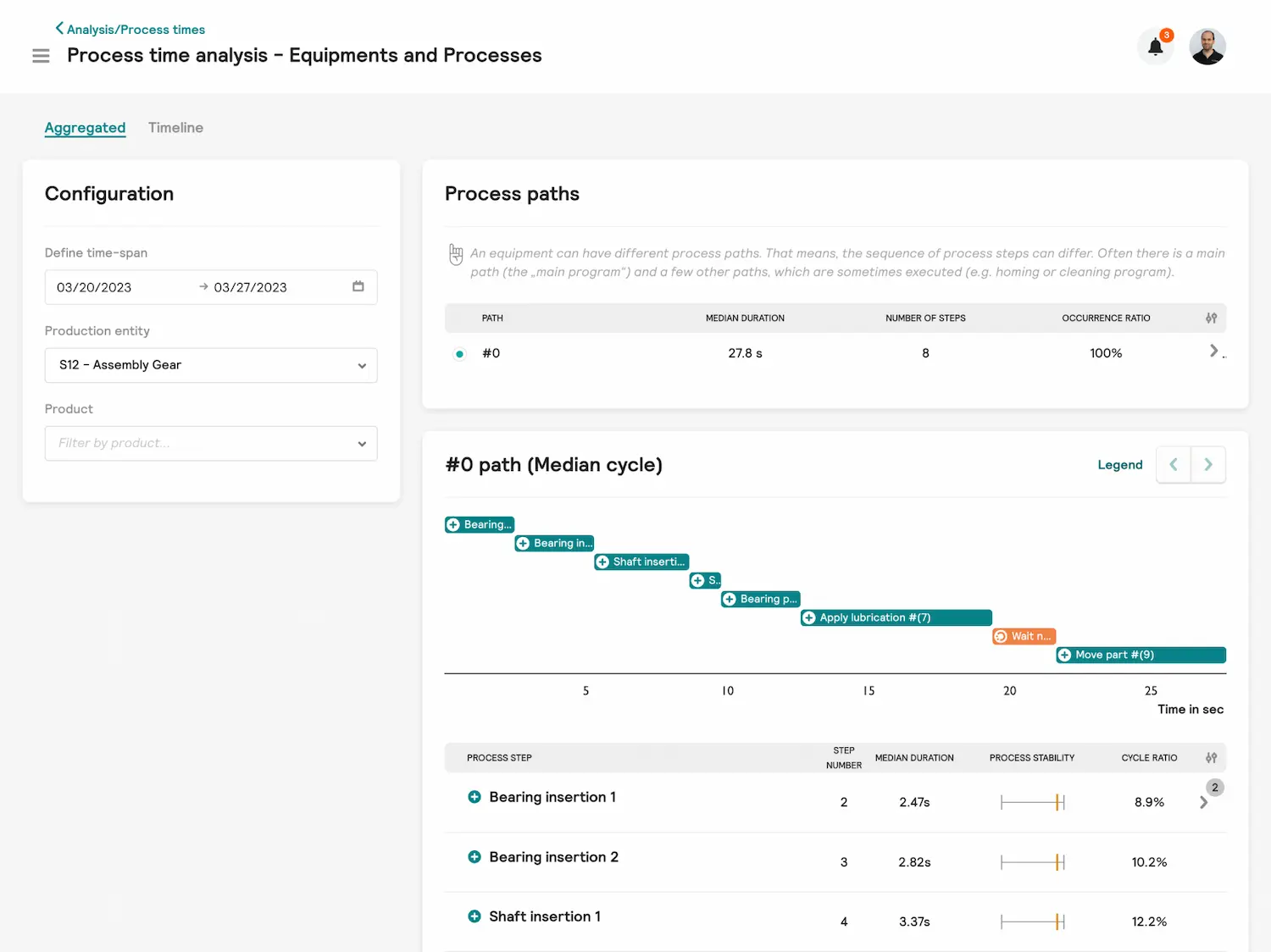
Shannon® - the operative shop floor assistance
- Turn your plant operators into experts: Shannon® provides information on the causes of malfunctions with situational solution suggestions and thus reduces downtimes through intelligent knowledge management
- 5 - 15 % increase in OEE through reduction of downtime and troubleshooting (MTTR)
- Knowledge management: building knowledge about actual machine behavior and solutions
- Addressing the shortage of skilled workers: Immediate support in solving the problem by proposing the expert knowledge.
.webp)
Hopper - the quality optimizer
- Automatically generated suggestions for parameter optimization help you reduce scrap and cycle time in the injection molding process.
- Increase output rate by significantly reducing scrap and cycle time
- Recommendations for detailed parameter adjustments taking into account all factors influencing the process
- Situational and automated recommendations available on smartwatch, smartphone and browser
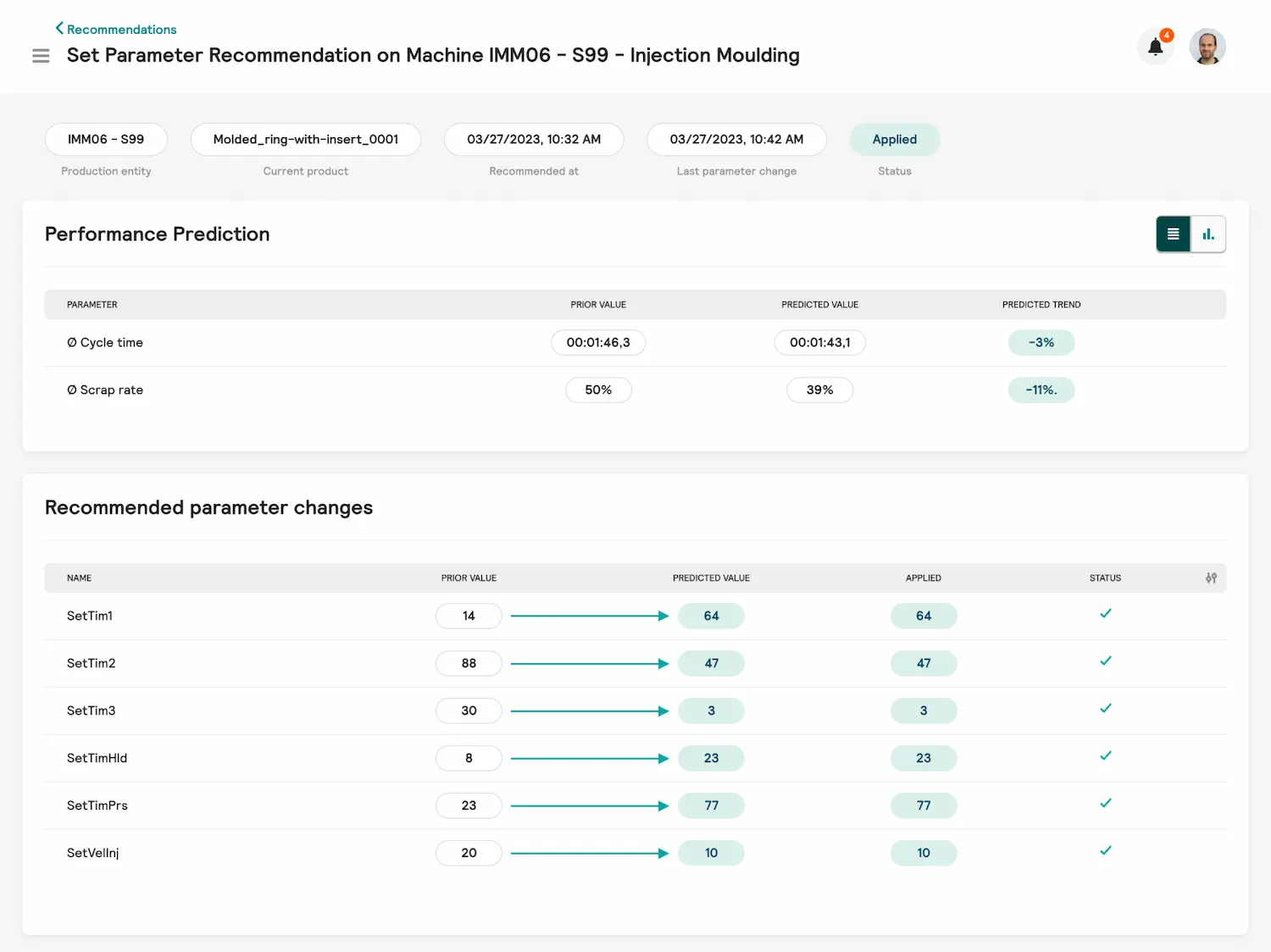
Request a free use case evaluation now.
- Product presentation with demo
- Roadmap for problem solving
- Holistic evaluation of the approach
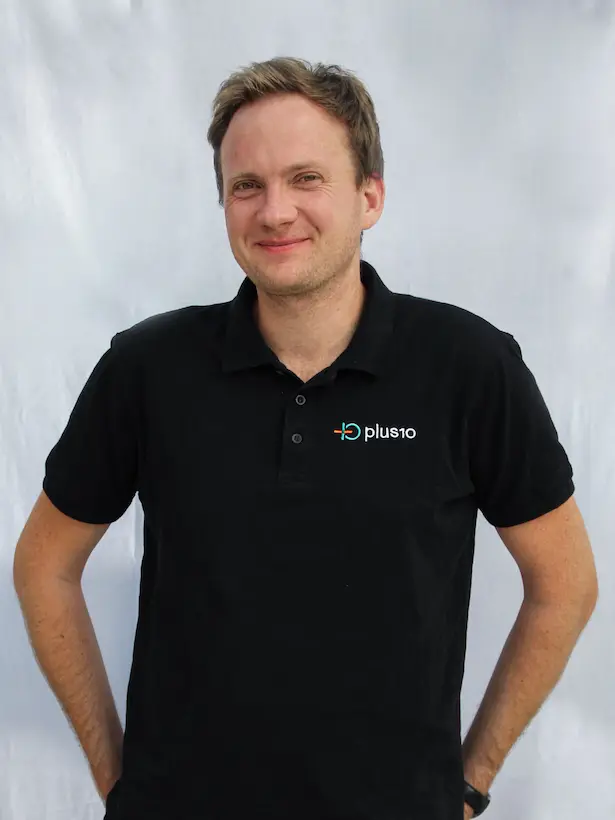