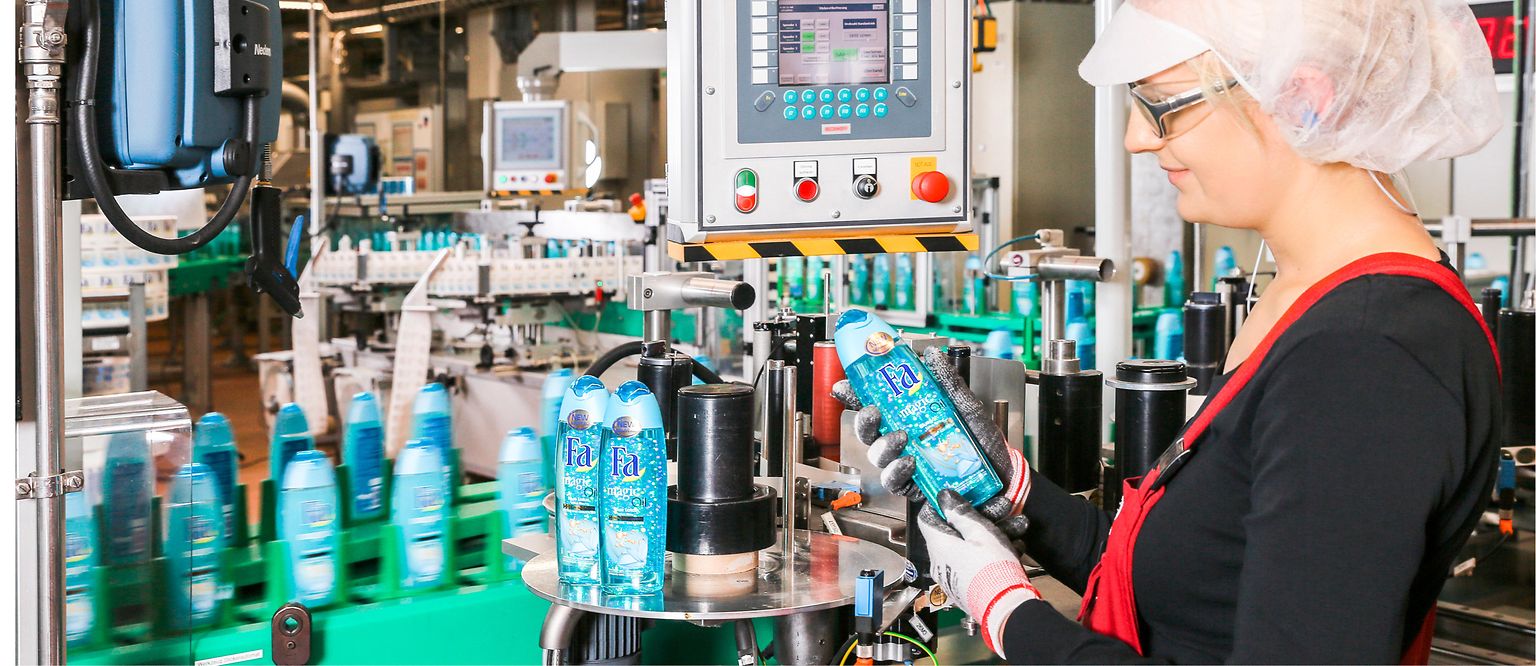
Cycle Time Optimization in Automated Machining
Similar or even identical machines with comparable processes often do not run at the same productivity level. To create more transparency about possible optimization potentials, plus10 offers the intelligent software tool Darwin.
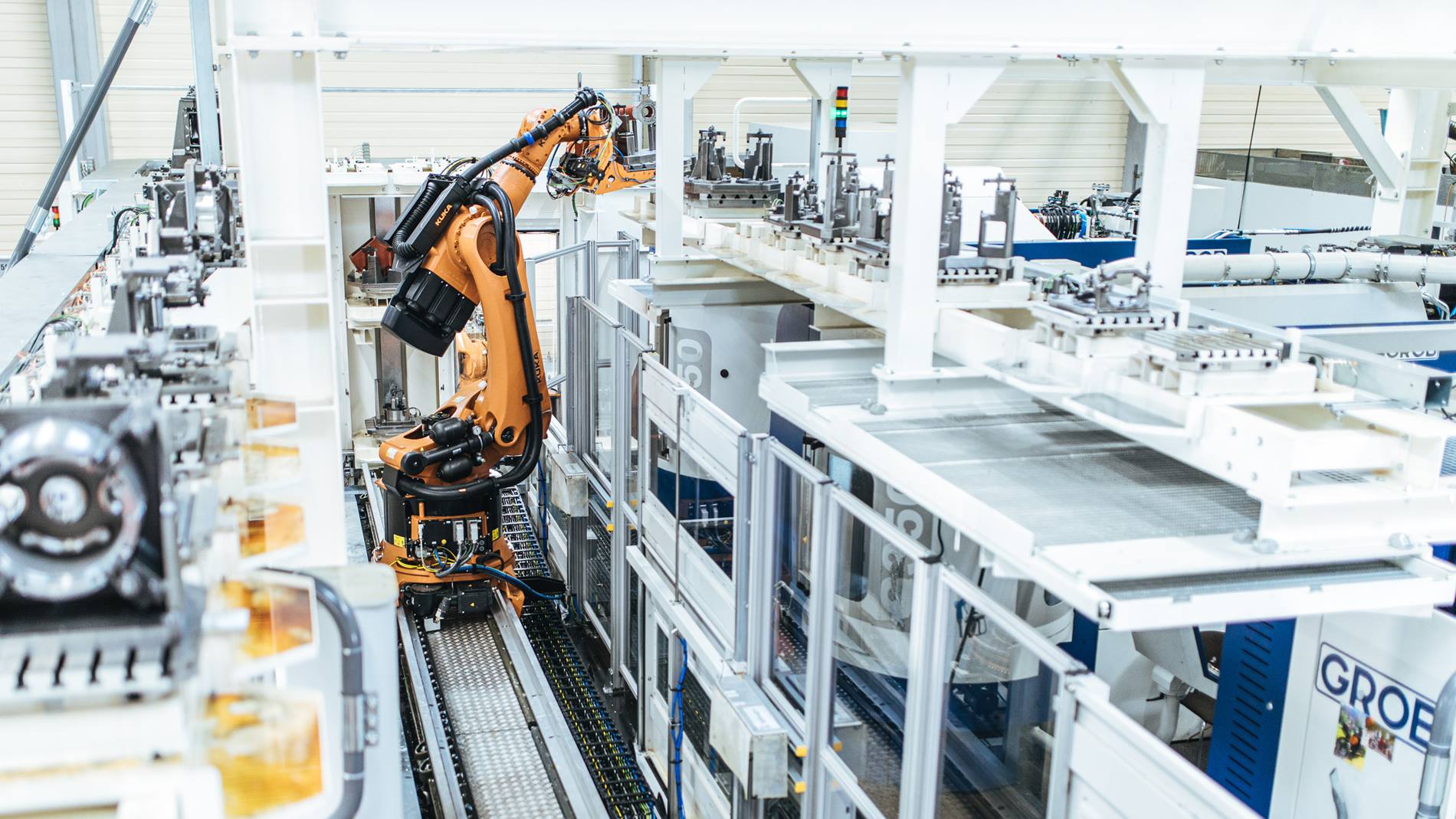
Similar or even identical machines with comparable processes often do not run at the same productivity level. Losses due to wear or varying programming result in an individual reduction of the machines' performance level. To create more transparency about possible optimization potential, plus10 GmbH, a Fraunhofer AI spinoff, developed the intelligent software tool Darwin. Darwin, the intelligent machine benchmark compares the individual process steps of several connected machines and learns a virtual ideal process to significantly reduce the technical non-productive times and thus the cycle time and maximize the OEE. The software has also already been able to uncover significant optimization potential in machine performance in automated machining.
Darwin - an intelligent and data-based machine benchmark for performance improvement
Darwin, the intelligent machine benchmark, offers several intelligent functions to identify concrete optimization potentials for several automated cutting machines incl. loading and unloading handling based on merged PLC, RC, and NC data in parallel to operation. In this way, it significantly increases the performance level of the machines. Based on the machine control data, the intelligent software tool generates a virtual ideal process from all connected machines and uses it to provide detailed optimization recommendations for reducing cycle time. In practice, Darwin achieves an increase in output by reducing the cycle time by 6 - 18 % per connected machine. The more complex the overall system, the more potential lies dormant here.
Field-proven AI tools - With high transparency to more productivity
In the fully automated production of complex machined blanks with 6-sided turn-mill machining, Darwin as an intelligent machine benchmark has already achieved significant success. Four identical machining cells, each with four milling machines, a lathe and automated loading and unloading handling, whose processes had already been highly optimized, were the subject of the study. Following cloud-based IT integration, Darwin was able to identify significant optimization potential for reducing cycle time with a focus on technical non-productive time. In the area of turning operations at the machining step level, for example, optimization potential of up to 15% was uncovered and directly linked to individual operations. This enabled the process experts to take direct and targeted action and subsequently measure the effectiveness of their measures directly.
For the senior process engineer, Darwin has already provided valuable insights into machine behavior and optimization potential: "With plus10's intelligent benchmark Darwin, we were able to compare tool change and tool machining times in detail at process step level across several dozen machines and derive optimization measures from them". On a lathe, for example, an optimization potential of 13.8 seconds was identified for the process step "finishing_rear", and the process duration of a tool machining on a milling machine could also be optimized by 8.1 seconds. In addition, optimization potential of up to 5.2 seconds was uncovered in loading and unloading handling - for example for the process step of loading the milling machine by a 6-axis robot. A maintenance engineer also reported that Darwin was able to make considerable progress in the coordination of the loading and unloading handling, which is shared by several machines via a long linear axis.
Compared to conventional optimization methods, Darwin uses the high-frequency internal data of all controllers involved (PLC, NC, RC) through a supplied interface and continuously and automatically generates concrete optimization recommendations for process experts in machining. This allows already optimized and utilized processes to be operated even more productively or expensive night and weekend shifts to be avoided.
Among other things to read at:
News from plus10.
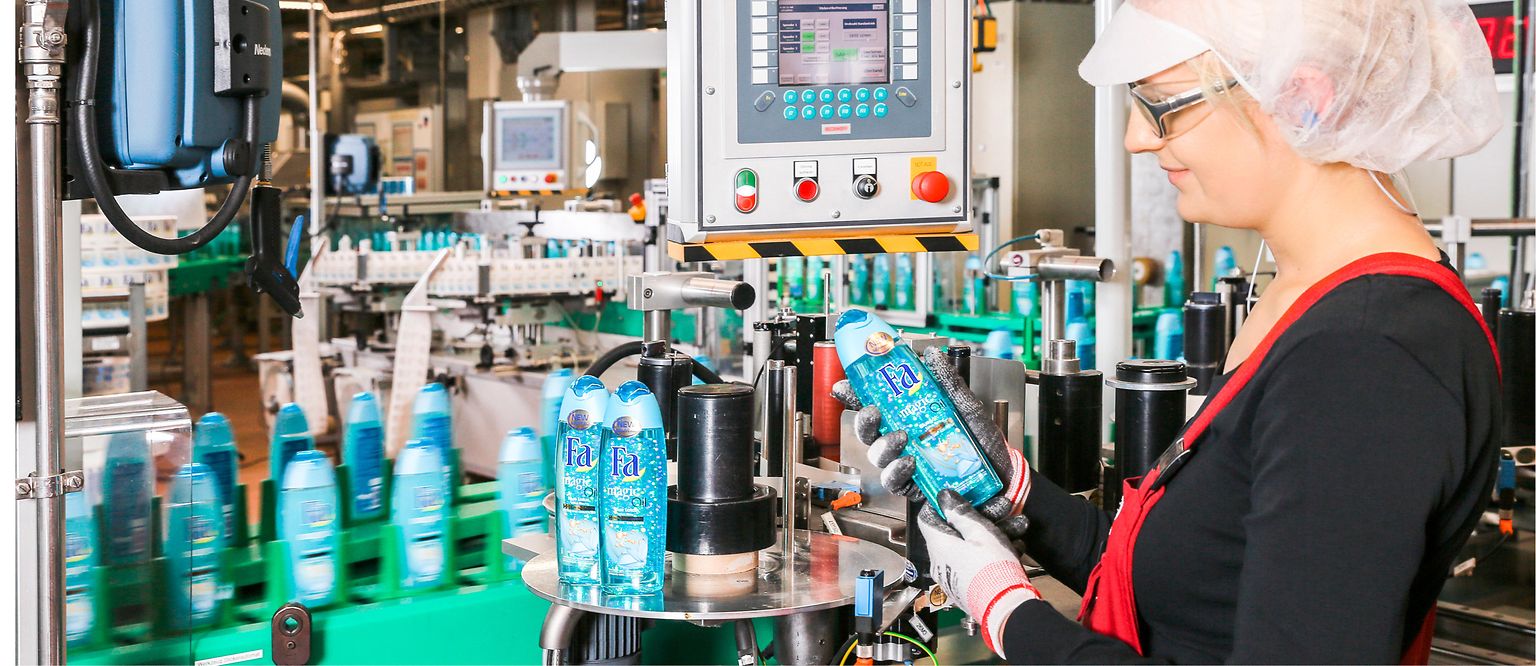
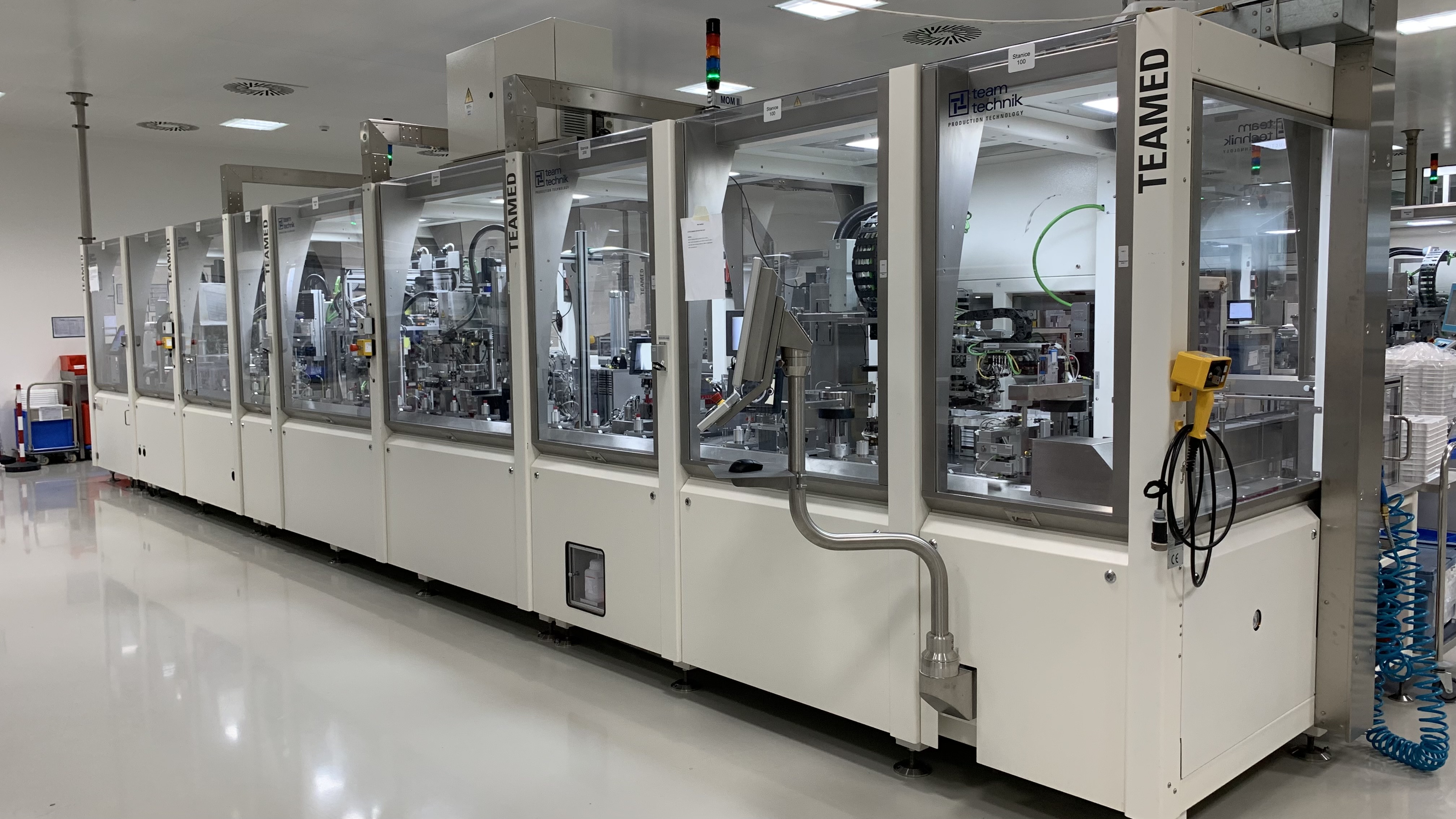
Microsoft Intelligent Manufacturing Award 2021 - plus10 and Haselmeier among winners
.webp)