DATA COLLECTOR - scalable, high-performance data infrastructure
Create a unified data base by connecting your machine controllers with the Data Collector - using a variety of protocols.
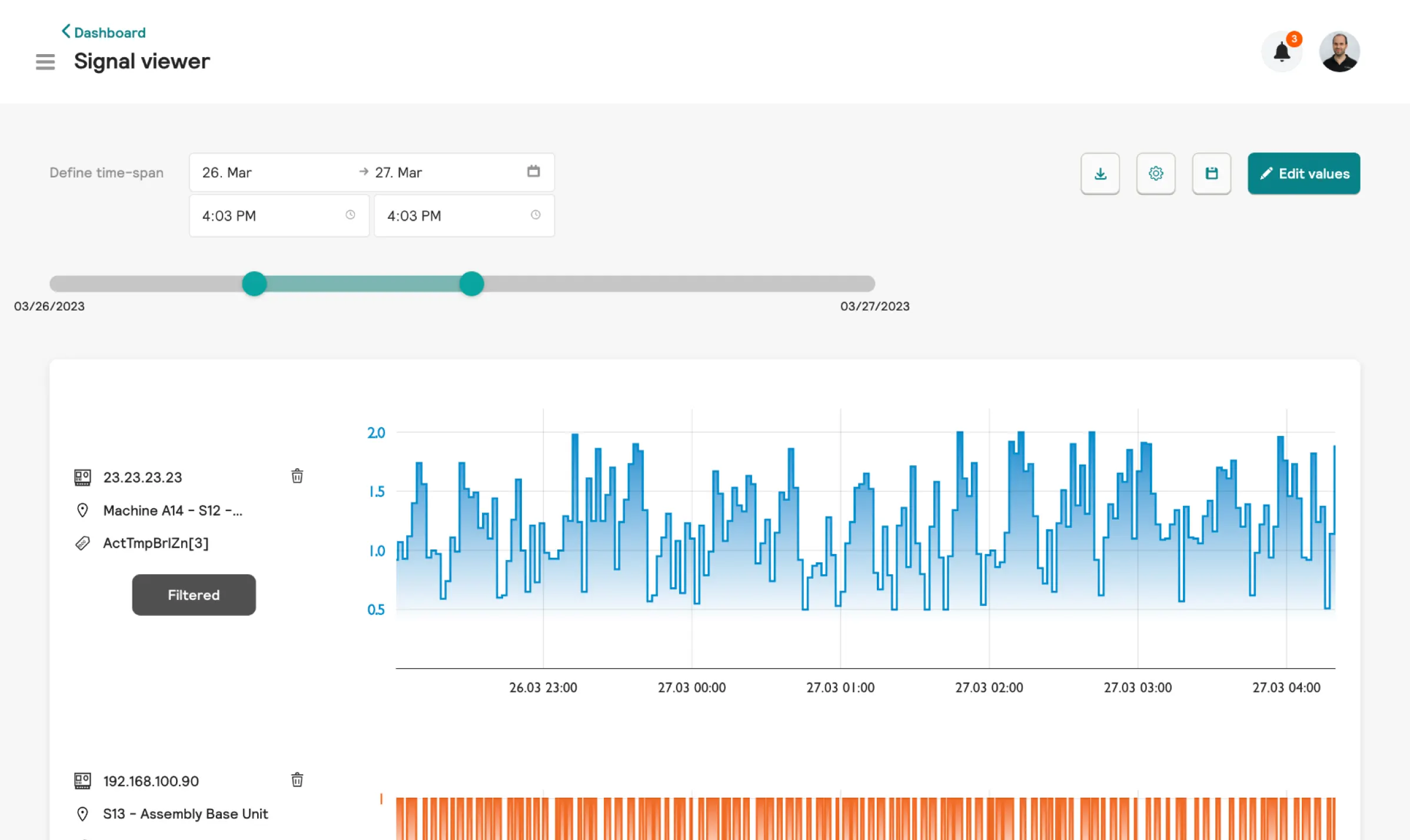
Connect inventory controls and collect machine data at high frequency
A high-performance data infrastructure for the acquisition and processing of machine data
Read machine data via a wide variety of protocols
Support for a wide range of protocols gives you full flexibility in connecting your machines. Read data from any source such as sensors, machine or robot controllers (PLC, RC, CNC).
- High-frequency sampling of signals in the millisecond range
- Support of proprietary protocols for the connection of controllers such as Siemens S7, Beckhoff or Codesys
Overview of all supported protocols
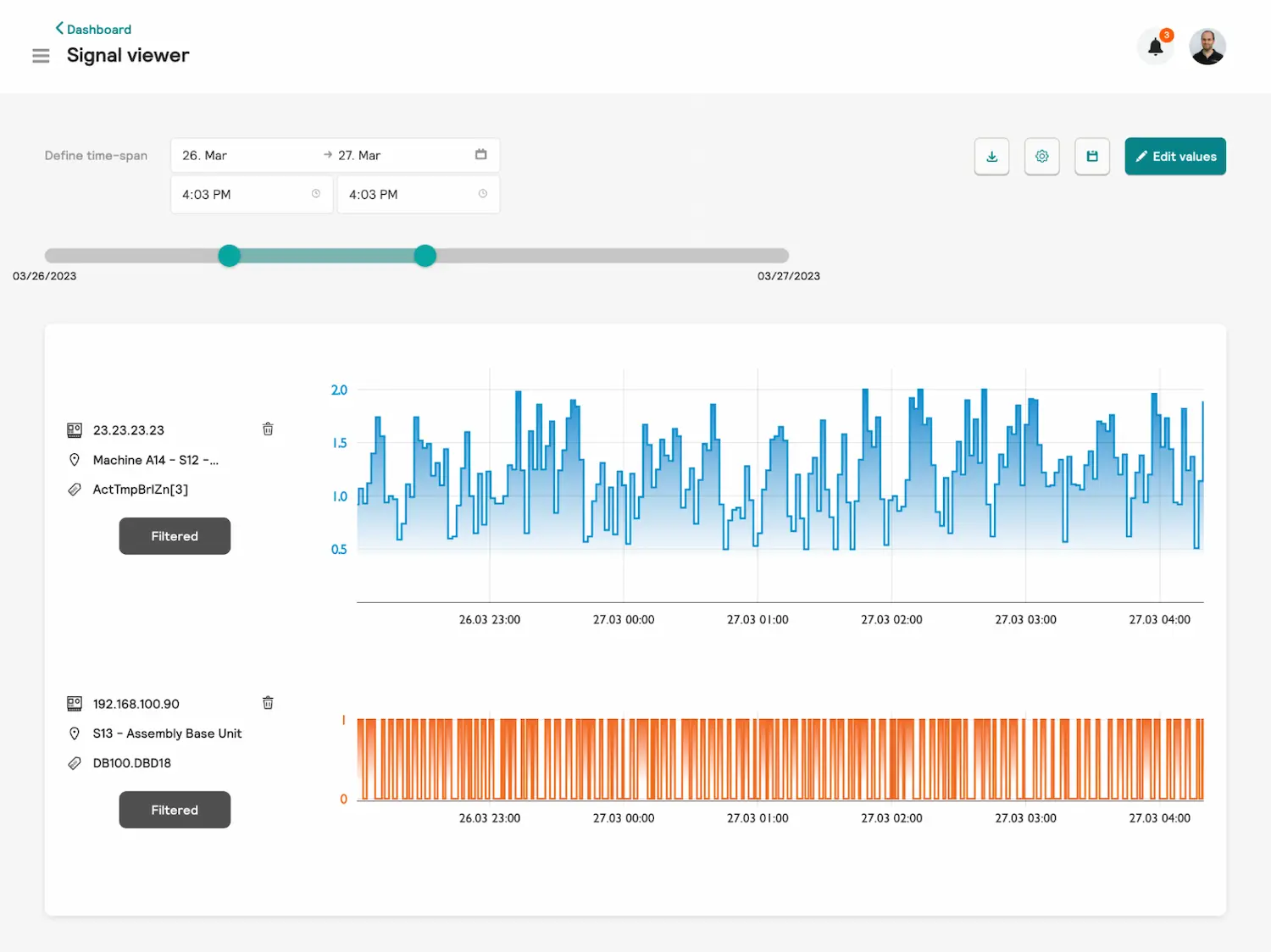
Scale your machine connections
Configure and manage any number of Data Collector instances on edge devices. Configure and monitor data connections through a central interface.
The tedious management of individual instances per edge device is no longer necessary.
= Reduction of the administrative effort of your data connections
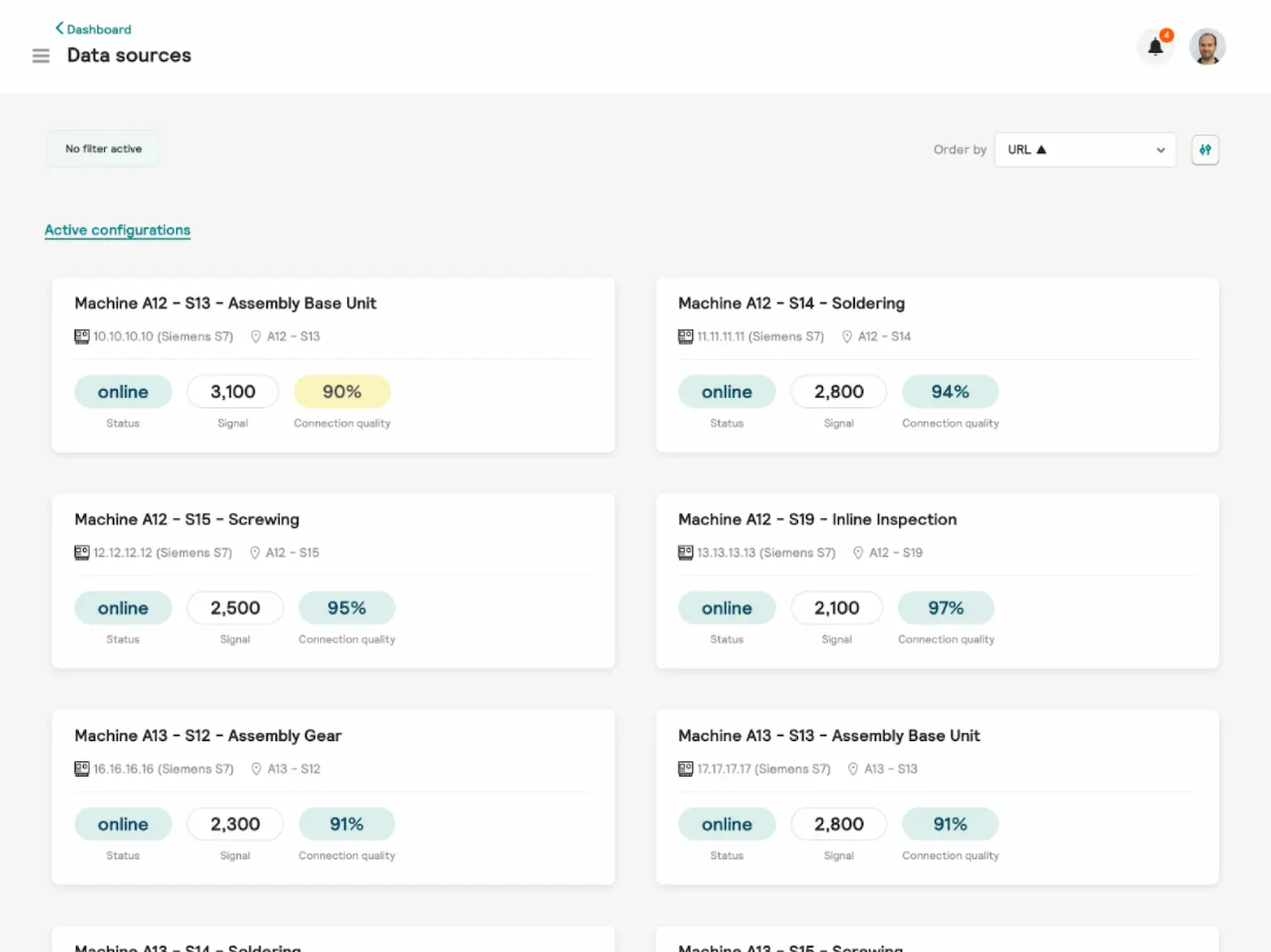
Use a central interface to provide machine data
The machine data is stored in a high-performance time series database.
Use the collected data with the help of an API (REST, streaming) and thereby make it available to other systems.
Data pre-processing functions simplify the use of data.
= The history of the raw data is easily and performantly available
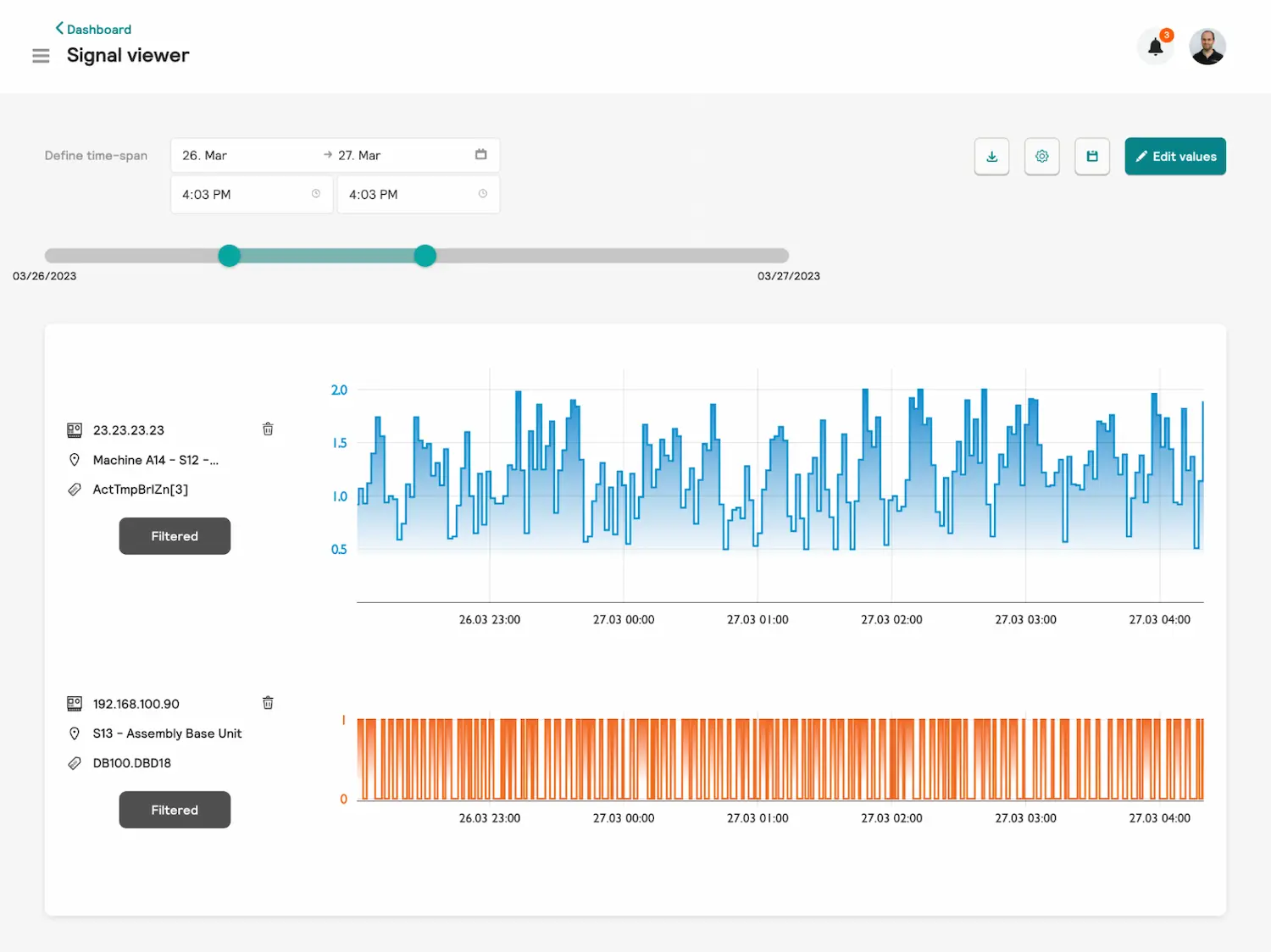
Advantages of DataCollector
Reading of high number of signals in the millisecond range
Brownfield integration through support of various protocols
Scalability through simple, central configuration
Data Collector solves these production problems.
- Central tool for collecting machine data from a wide variety of sources on the shop floor
- Connection of various PLCs from different manufacturers and generations
- High-frequency acquisition of machine data without influencing the production process
- Acquisition of data without adaptation to controls themselves
- Minimum network traffic
- Reliable data through synchronization of data sources
- Secure communication
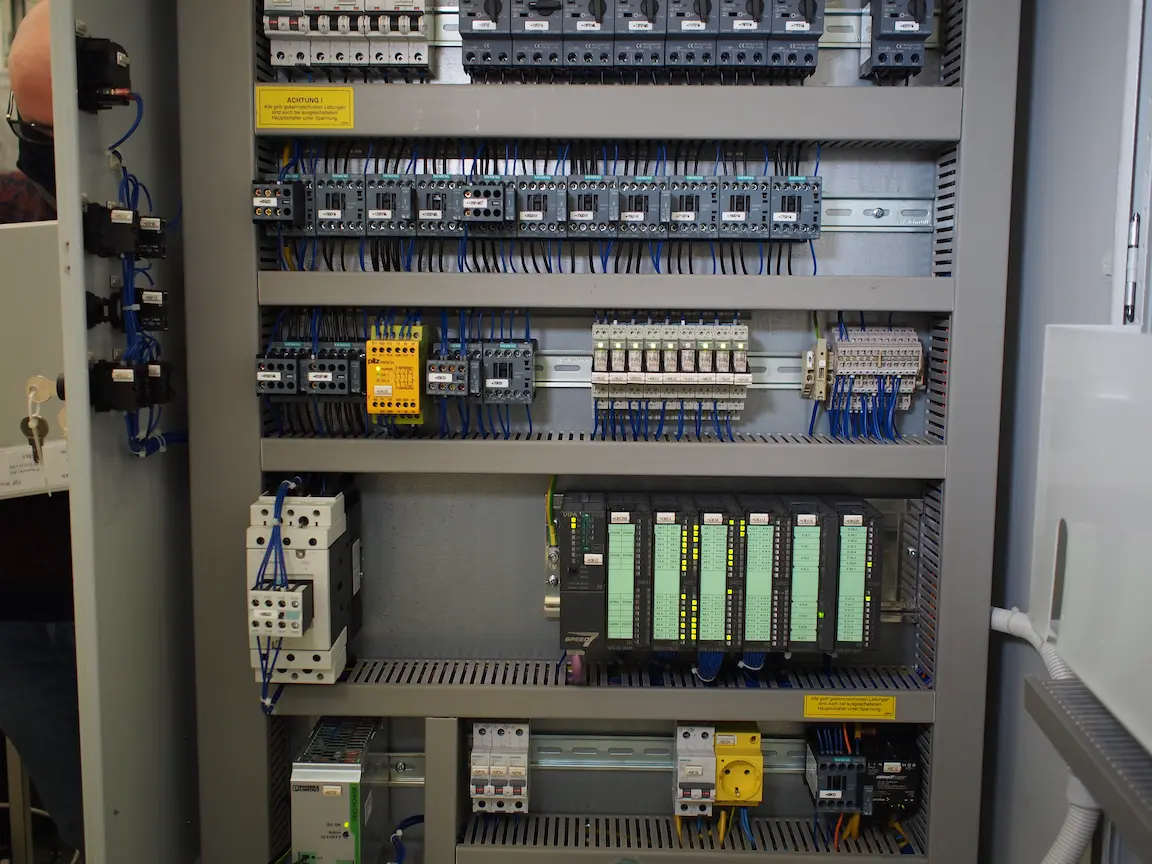
All features of Data Collector
Reading machine data
Reading machine data
The DataCollector supports a wide range of protocols for reading machine data.
In addition to machine-to-machine protocols such as OPC-UA, a strength of the DataCollector is its support for a wide variety of proprietary protocols (such as Siemens S7 or Beckhoff TwinCAT).
The reading of the machine data is designed for performance in order to be able to read data at the highest possible sampling rate.
Central management
Central management
Manage and configure any number of DataCollector instances via a central interface (web application or API).
You don't have to configure each DataCollector individually and laboriously access each edge computer.
By reducing administrative overhead, DataCollector can be rolled out across entire factories at scale.
.webp)
Data preprocessing
Data preprocessing
The recorded raw data is pre-processed directly "at the edge". In this way, we increase the performance of data provision and reduce the data traffic generated.
Feature Engineering
Feature Engineering
Transform raw data with complex rules to create new statements.
This way you can apply a mathematical operation on a signal to give it a new meaning.
Features are calculated live and can be accessed via a streaming and REST interface.
.webp)
Signal Viewer
Signal Viewer
The Signal Viewer displays signal values. This allows you to track the value progression over time and draw conclusions about the process behavior.
In addition, statistics and histograms give you further possibilities to understand the signal behavior.
.webp)
Time series database
Time series database
The signal values are stored in a high-performance time series database so that you can access the historical signal values at any time.
You can retrieve the data via an API.
API
API
Use the REST and streaming API to interact with the DataCollector. Retrieve signal values or adjust the configuration programmatically via a standardized interface.
This allows you to integrate our solution with existing systems.
Interface
Security
Add ons
Supported systems and interfaces
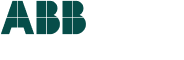
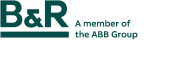
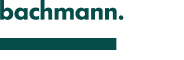
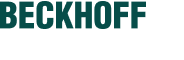
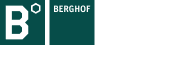
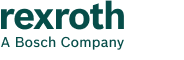
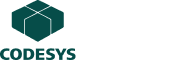
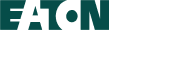
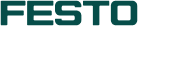
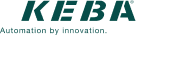
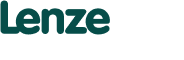
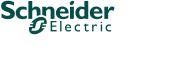
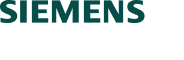
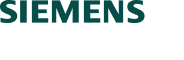
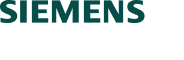
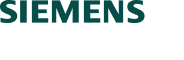
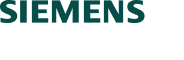
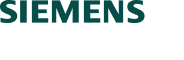
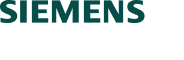
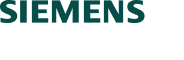
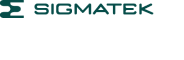
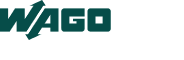
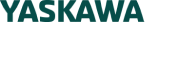
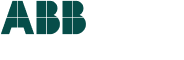
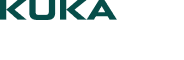
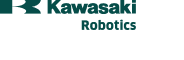
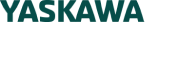
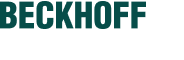
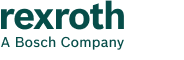
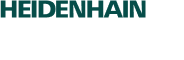
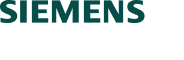
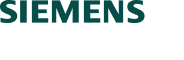
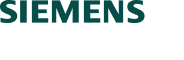
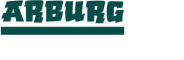
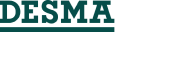
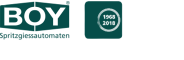
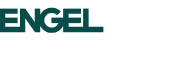
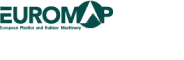
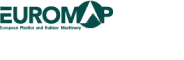
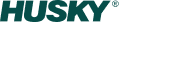
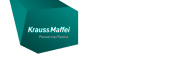
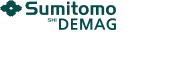
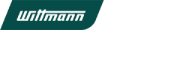
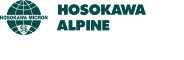
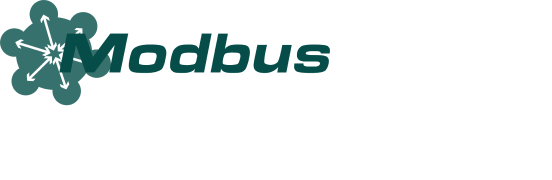
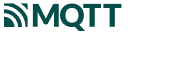
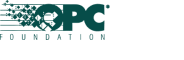
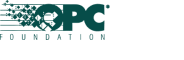
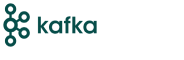
Use our high-performance edge device.
- Modern hardware with Intel i7 processors (up to 8 cores) and up to 32GB memory
- Variety of (network) interfaces
- Industry-ready for DIN control cabinet integration
- Ready configured delivery with Data Collector software
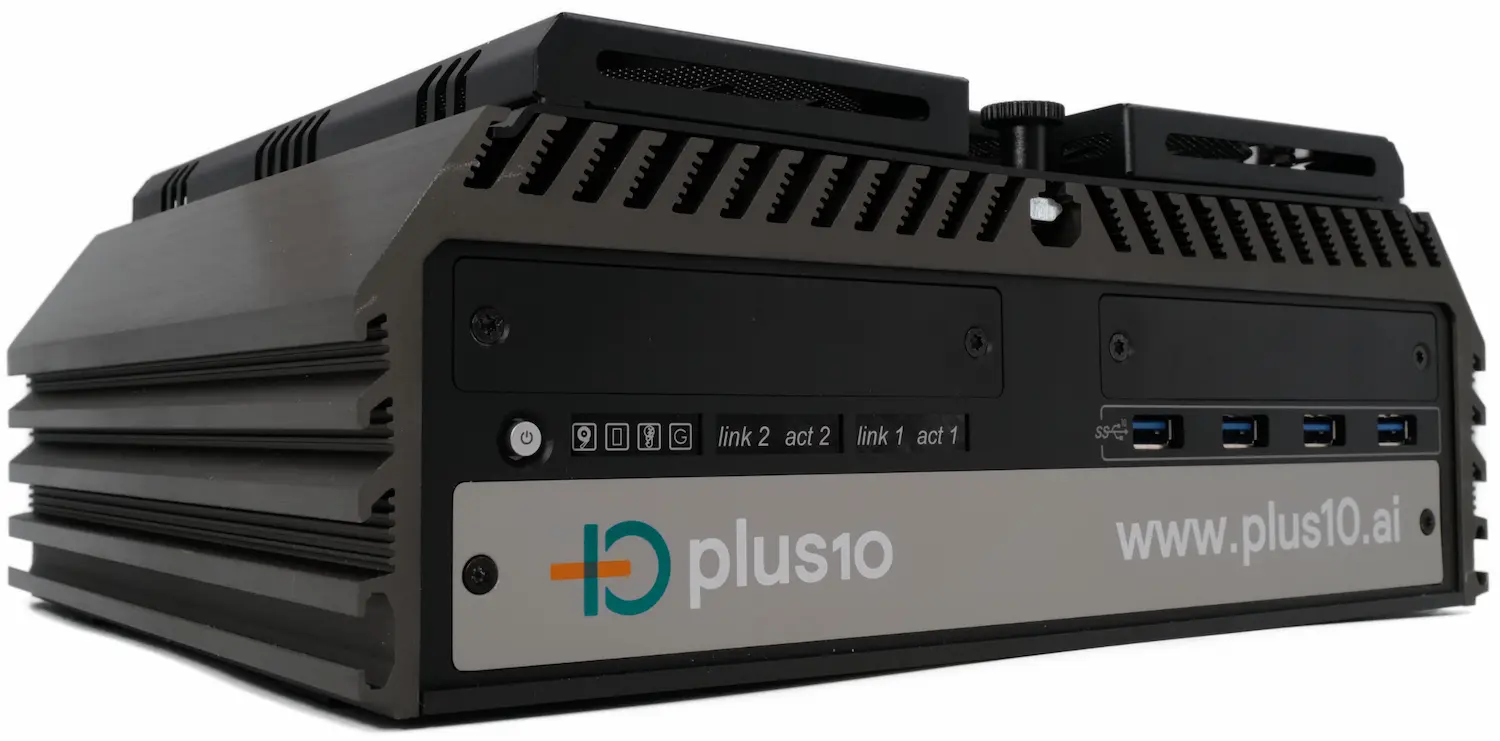
A scalable IT architecture with central backend and any number of edge deployments
The plus10 IT architecture consists of the central Software as a Service instance and any number of edge computing units that collect data from machine controllers.
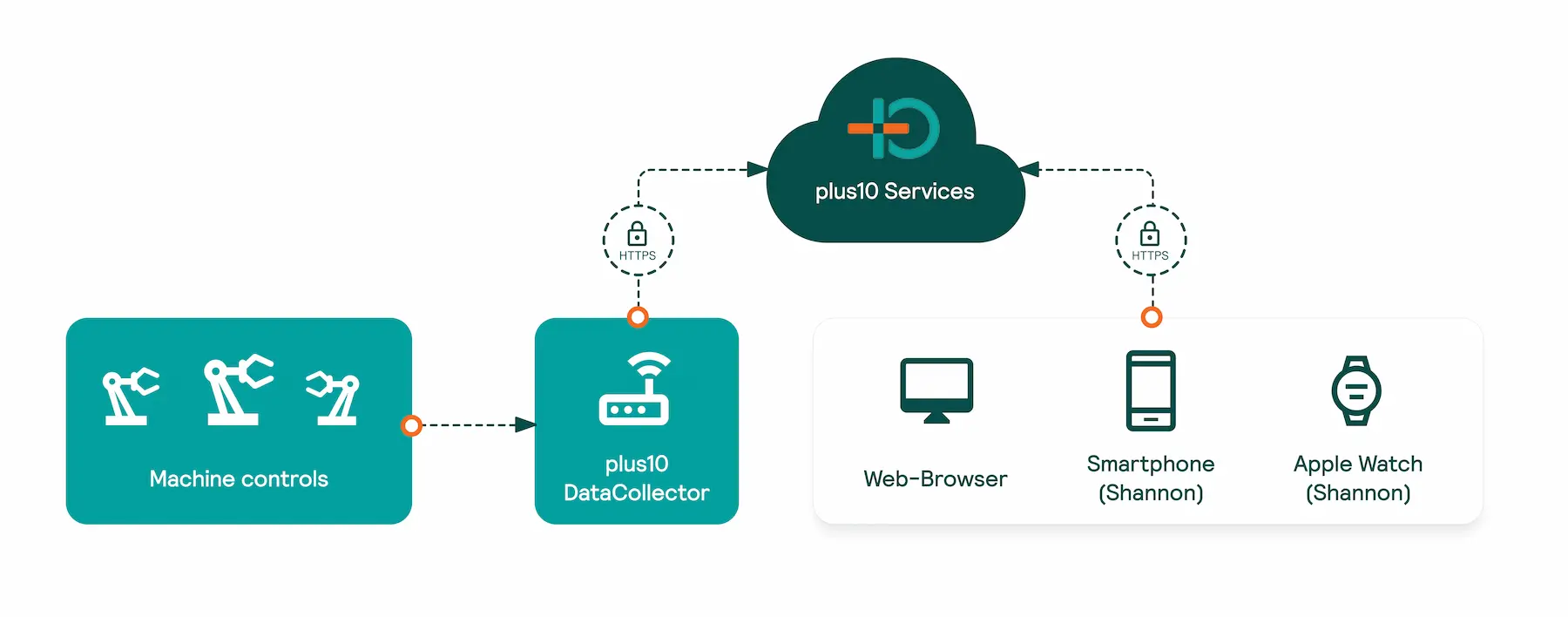
What our customers & partners say
Request a free use case evaluation now.
- Product presentation with demo
- Roadmap for problem solving
- Holistic evaluation of the approach
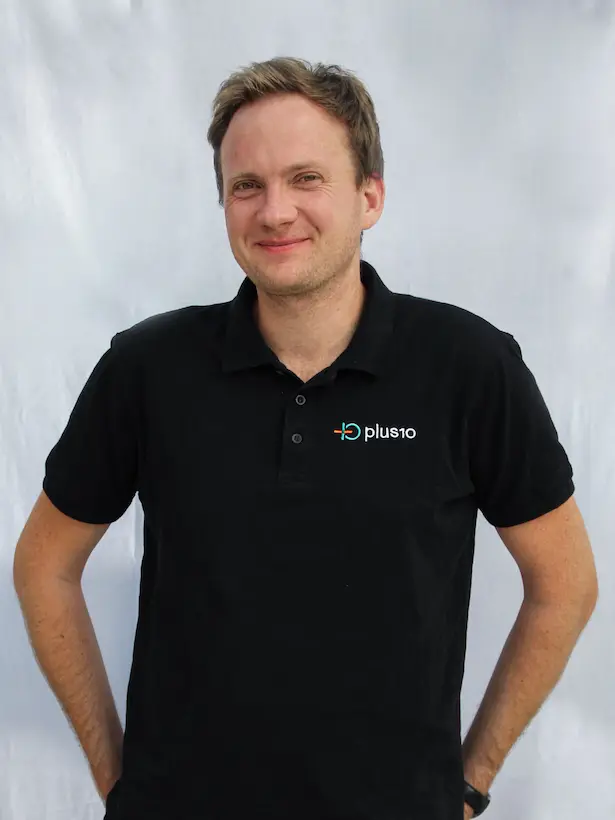
More products from plus10
You have questions? We have answers!
And if you have any further questions, please feel free to contact us.
plus10 collects the data directly from all integrated machine controllers (PLC, NC), robot controllers (RC), etc. of a production machine or from all controllers integrated in a production line. To do this, we use our plus10 DataCollector to acquire high frequency data from all PLCs, NC and/or RC involved. So far we can collect high frequency machine data with different manufacturer specific PLC protocols and we are continuously adding more controllers. Find out more about the controllers we support here or ask us about compatibility with your specific controller type.
If you already have a powerful IT infrastructure installed in your factory, we also offer the connection to your middleware.
Basically plus10 collects and processes all data of the machine control (PLC) of the production machines or the production line in high frequency. The high sampling rate (we are talking about milliseconds) is necessary to detect and assign the causes of problems and not only their consequences. In some cases the RC and NC data of e.g. handling robots are additionally required. In the standard case, no additional sensors or cameras need to be installed.
The plus10 software tools are flexible in terms of IT infrastructure. Data acquisition and pre-processing runs continuously locally, e.g. on an Industrial Edge Device or a virtual machine within the machine control network. For the next processing step, plus10 adapts to your preferred solution: We can provide a cloud environment for our software tools or they can run on a virtual machine on-premise in your existing in-plant data center. Both are possible and we have experience with both options.