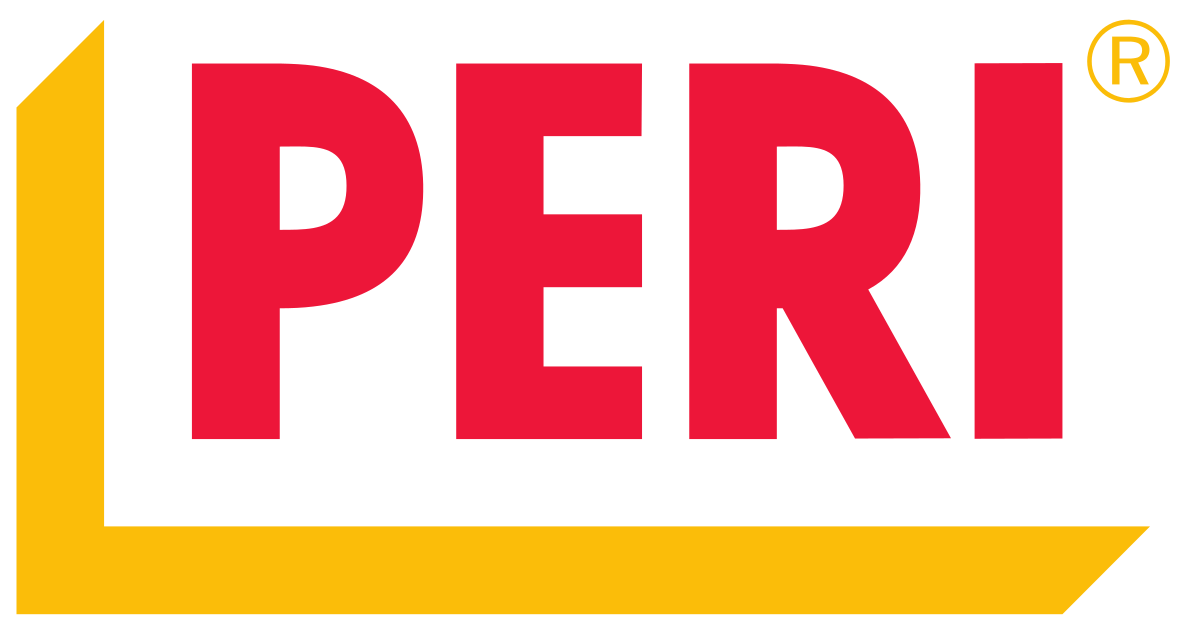
Shannon® at Peri
Fully automated production line for safety-critical scaffold decking consisting of 34 process steps with 11-second cycle times.
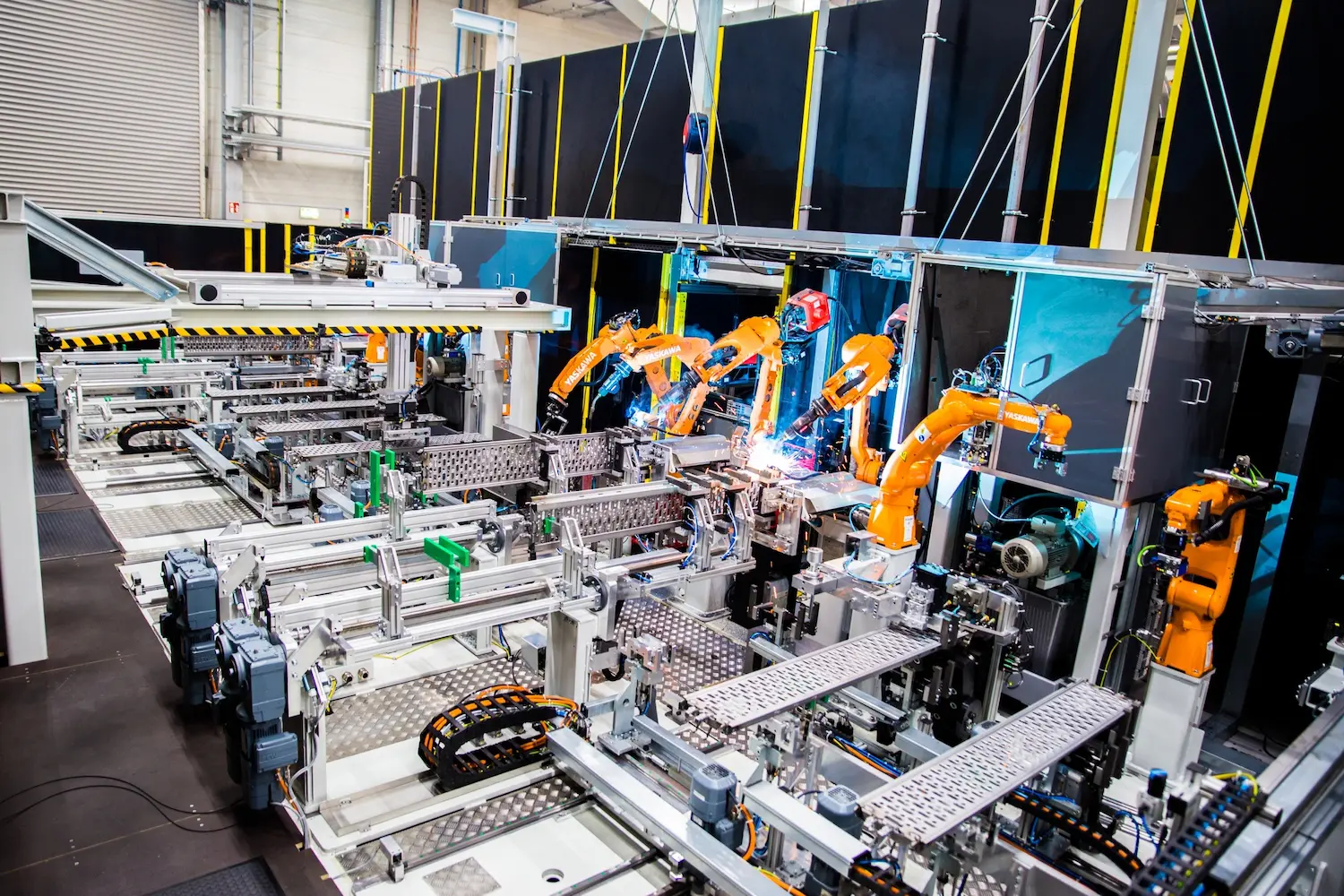
Scope
The use case in numbers
over 50 solutions to problems
generated for disruptions during onboarding phase
21 Processes
which leads to significant product variation & quality
36 Welding robots
and other machine controls are connected
The goal
- Implementation and operation of Shannon® in multi-shift operation on a fully automated production line for scaffolding decks
- High-frequency connection of all machine controllers involved (various PLCs, RC, motion, welding and test controllers) as a fused live data basis
- Knowledge management and documentation of the most effective troubleshooting procedure in the event of an incident
"With Shannon, we were able to generate data-based transparency on all relevant machine malfunctions, including localization and prioritization, after the implementation phase. In addition, machine downtimes could be analyzed live at signal level. The plus10 team proved to be extremely competent and supportive."
Daniel Spanfellner
Smart Factory Expert, PERI
The solution
- Real-time visibility into current and past disruptions
- Prioritization of relevant disturbances to causal problems
- Faster cause finding for machine downtimes with integrated signal viewer for all controllers
- Generation of over 50 solutions during implementation phase for situational problem solving with Shannon®.
- Intensive support of the software introduction at shop floor level in all shifts by plus10
- Cloud edge-based IT infrastructure for high-frequency yet scalable integration
Request a free use case evaluation now.
- Product presentation with demo
- Roadmap for problem solving
- Holistic evaluation of the approach
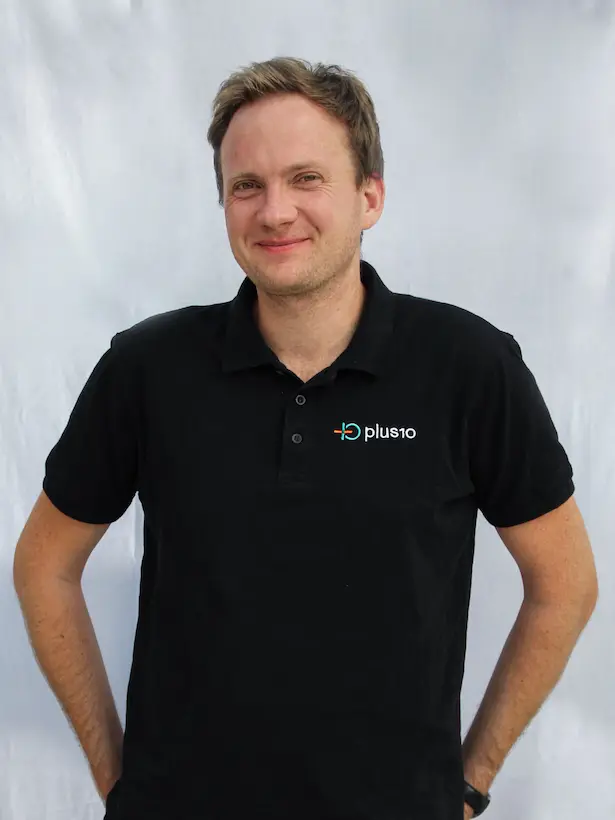
Felix Müller
Sales
Success Stories