Darwin at Schwarzkopf
Fully automated and interlinked filling and packaging line for consumer goods (350 products/min). Several PLCs of different manufacturers and generations involved.
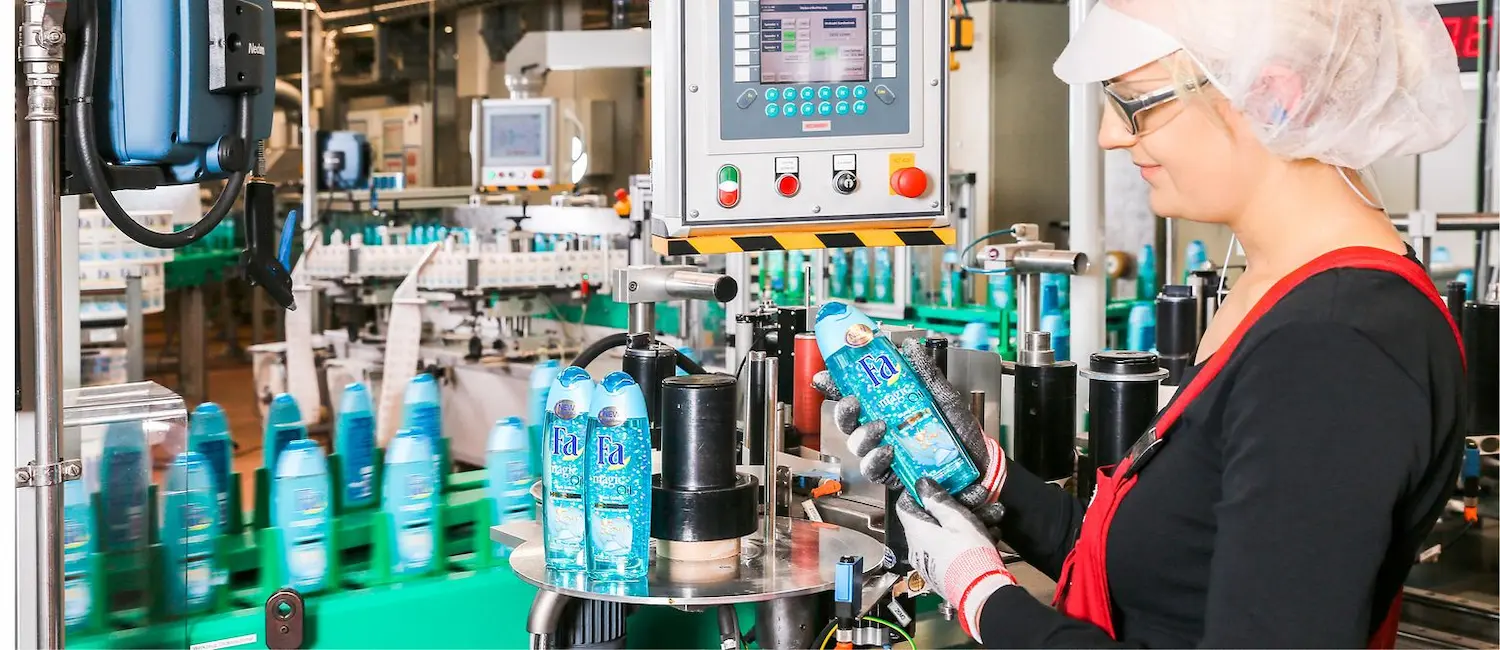
Scope
The use case in numbers
Up to 17% potential
identified for increasing throughput
350 products per minute
made on production line
12 process steps
with different PLCs were considered
The goal
- High-frequency data connection of all involved machine controls (PLC) incl. retro-fits as data basis
- Implementation of a data-based downtime and cycle time analysis at station level
- Output increase by increasing the technical availability and the performance level of the plant
- Increase output by building a quantitative influence and impact simulation of different buffer scenarios and alternatives to the higher-level control logic between stations based on the data from plus10.
"With the software from plus10, we were able to benefit from detailed transparency about downtimes and process times already during the implementation phase. The signal-based root cause analysis by the Signal Viewer as well as the detailed fault analysis on station level were particularly profitable. With the help of the simulation based on the data, it was possible to define a package of measures to increase output."
Lutz Kaiser
Plant Engineer, Schwarzkopf & Henkel Production Europe GmbH & Co. KG
The solution
- Detailed transparency of downtime per shift at station level for effective shift handover and basis for conceptual optimization
- Detailed transparency of cycle times at station level as a basis for conceptual optimization
- Faster root cause identification in the optimization process and during downtimes thanks to visualization of the signal behavior using the integrated plus10 Signal Viewer
- Additional simulation based on the high-frequency machine control data
Request a free use case evaluation now.
- Product presentation with demo
- Roadmap for problem solving
- Holistic evaluation of the approach
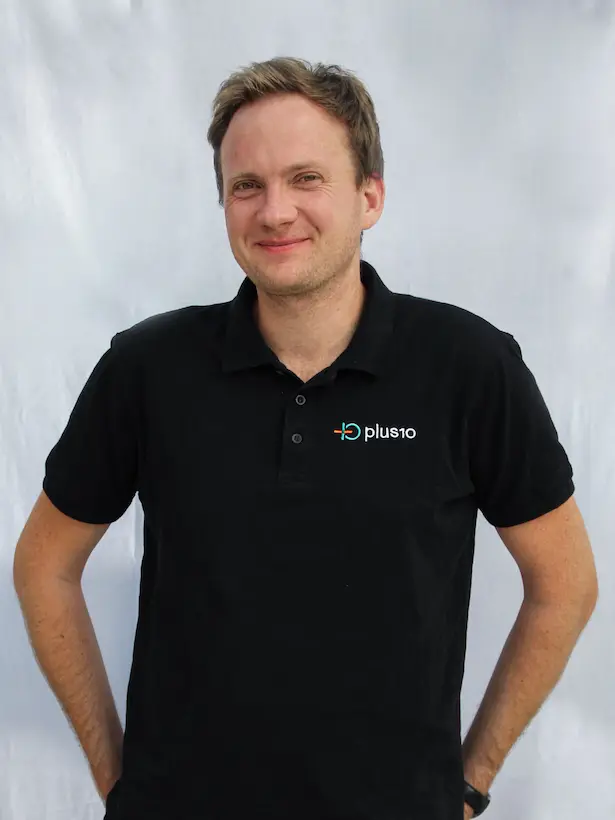
Felix Müller
Sales
Success Stories