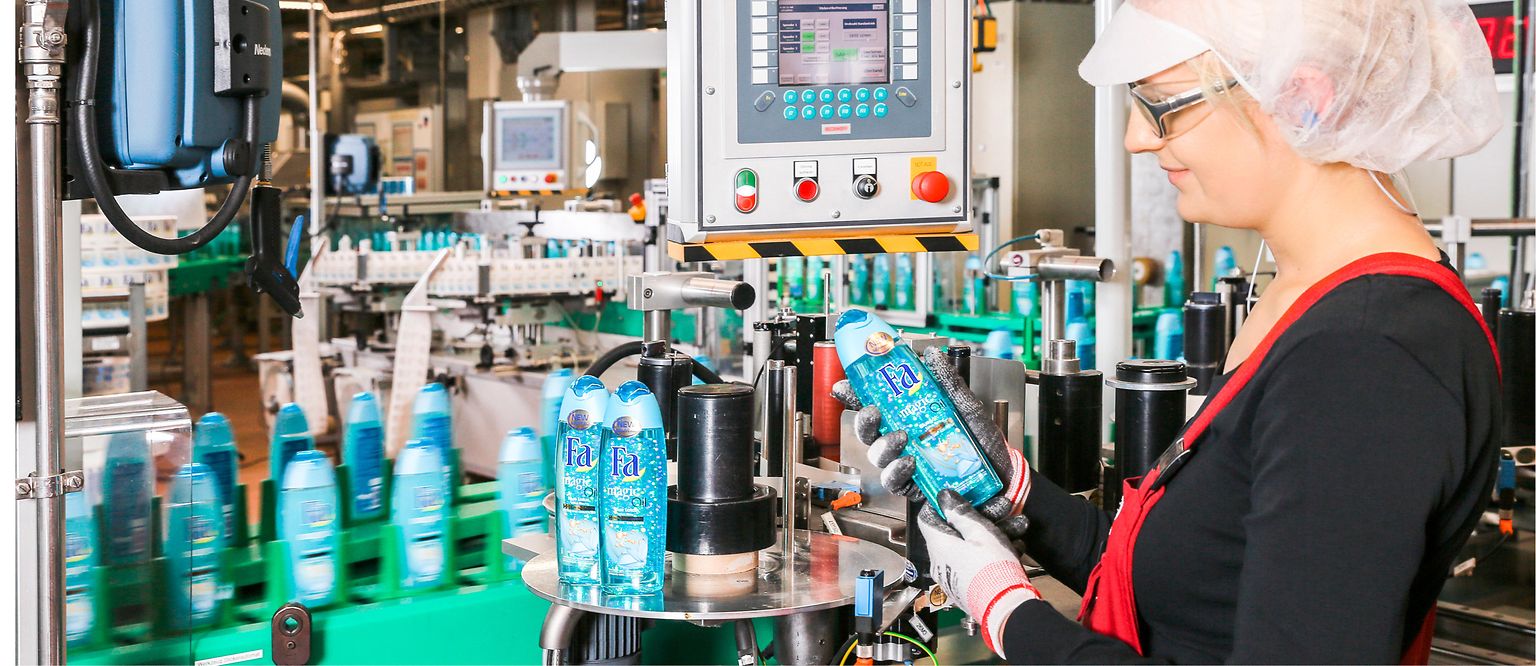
Allow machines to learn from each other across manufacturers
plus10 is conducting application-oriented research together with the Southern German Plastics Center SKZ as part of the DarWIN project on new AI-based optimization tools for injection molding machines. The aim is to develop continuously learning models in a practical manner that adaptively enable higher quality with shorter cycle times around the clock
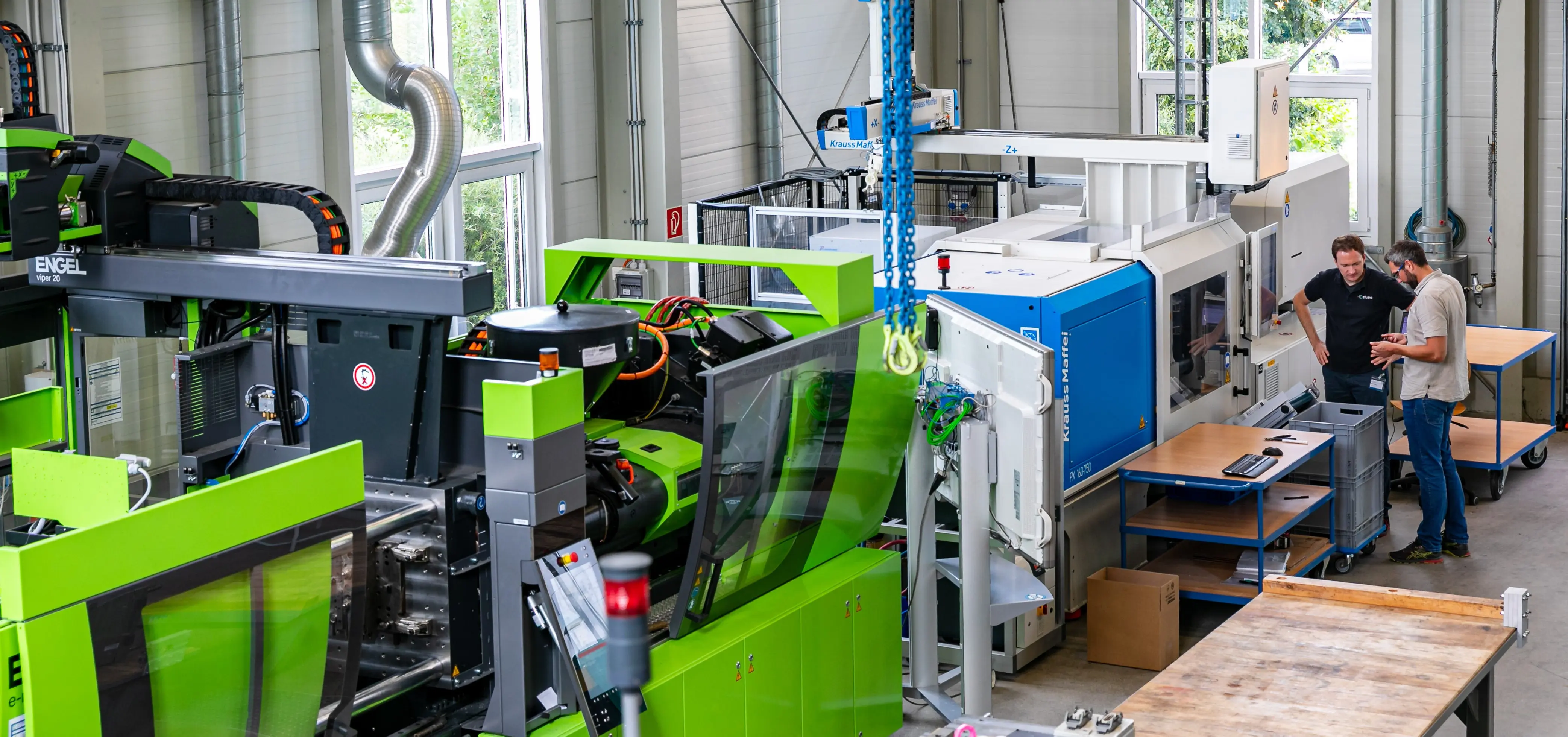
DarWIN research project - plus10 and Demag work on the future of injection molding
The Fraunhofer spin-off plus10 is conducting application-oriented research together with the Southern German Plastics Center SKZ as part of the DarWIN project on new AI-based optimization tools for injection molding machines. The goal is to develop continuous learning models in a practical manner that adaptively enable higher quality with shorter cycle times around the clock. To this end, machines from different manufacturers are included and generalization strategies for overarching learning phases are designed. A final series of tests has now also been carried out on machines from the company Sumitomo (SHI) Demag.
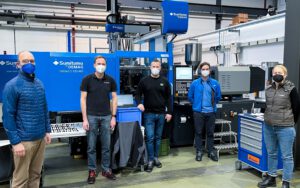
Since mid-2020, the research and development work and, since 2021, also the test series of the Fraunhofer spin-off plus10 and the SKZ Plastics Center have been running for the DarWIN research project. With this AI project, detailed behavior models of injection molding machines are learned on the basis of high-frequency machine data. The transferability of pre-trained machine learning models allows individual machines to learn from each other. This means that behavior models of a specific machine do not have to be completely relearned each time, but are only adapted to the machine and the product currently being run in a small adaptation phase. These behavior models suggest optimized process parameters for the next machine cycle in order to be able to produce in the shortest cycle time and without rejects under the currently prevailing boundary conditions, such as raw material characteristics and environmental conditions. The special feature of the DarWIN project is that machines from different manufacturers learn from each other. The behavioral models can therefore be transferred to machines of similar size and technology, irrespective of the manufacturer.
AI trials on Sumitomo (SHI) Demag machines
Recently, plus10 and SKZ also conducted these test series on Sumitomo (SHI) Demag machines. The high-frequency machine connectivity of the Sumitomo (SHI) Demag machines makes it possible to train plus10 algorithms on the machines. This allows the equipment to continuously learn, eliminating scrap and ensuring that the machines are always operating at maximum productivity. One advantage of Sumitomo (SHI) Demag machines here is that their control systems enable high-frequency, near-real-time communication in the millisecond range. The continuously learning AI-based optimization tools can thus be easily implemented and used in the installations; the machines are "AI-ready", so to speak.
The test series in the Sumitomo (SHI) Demag Technical Center not only contribute to the optimization of injection molding machines, but also simultaneously serve interface development and continuous testing and further development of AI-based software tools. By providing a real test environment, SHI proactively takes up innovative topics and ideas for its machines and actively helps shape the future of injection molding.
Research results relevant for sustainable plastics industry
The results of the research project are also of great importance for sustainable plastics processing. The plus10 technology makes it possible to process even sensitive or heterogeneous materials, such as thermoplastic post-consumer recyclates or rapidly crosslinking elastomers, in a process-stable manner. The findings thus support a functioning circular economy in plastics processing.
The "DarWIN" research project (BMBF funding code 01IS20066) is funded by the German Federal Ministry of Education and Research (BMBF) and ended on December 31, 2021. Currently, the results obtained are being processed and are flowing into software development internally at plus10. The publication of the final results is planned for the end of 2022, as well as further activities and live demonstrations of the development results at specialist events such as the "Digital Injection Molding" meeting at the SKZ in Würzburg together with the SKZ.
Among other things to read at
- Plastverarbeiter | Joint research project for a sustainable future of injection molding
- K-Current | Sumitomo (SHI) Demag: How machines learn from each other across manufacturers
News from plus10.
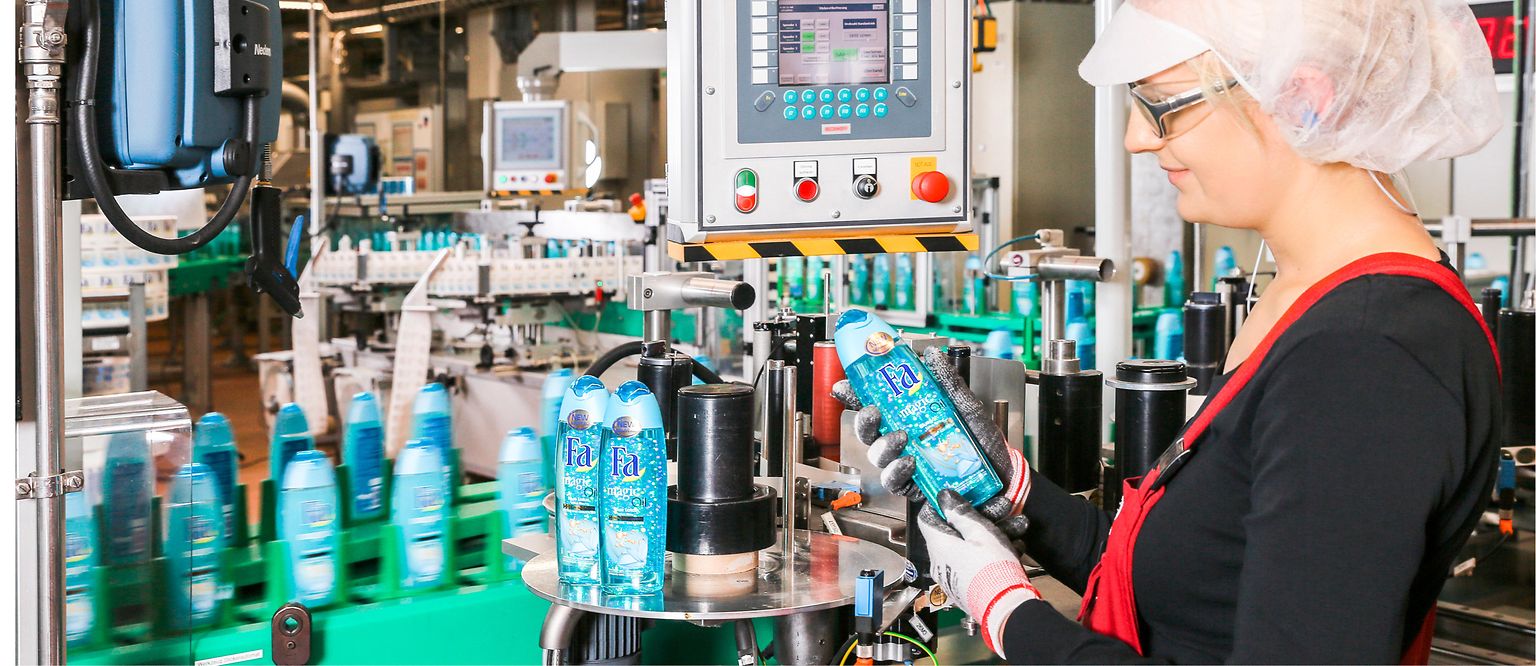
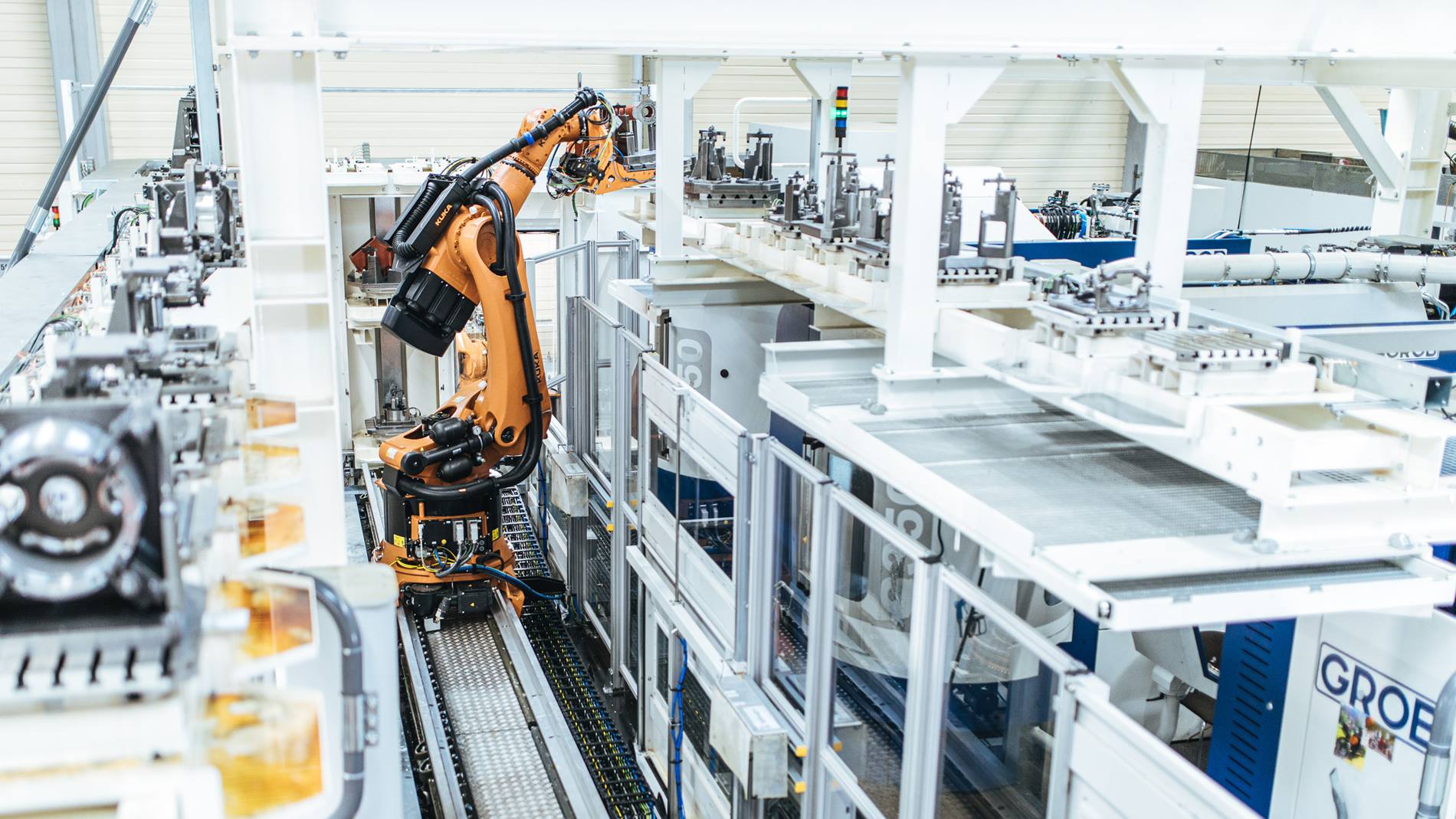
Cycle Time Optimization in Automated Machining
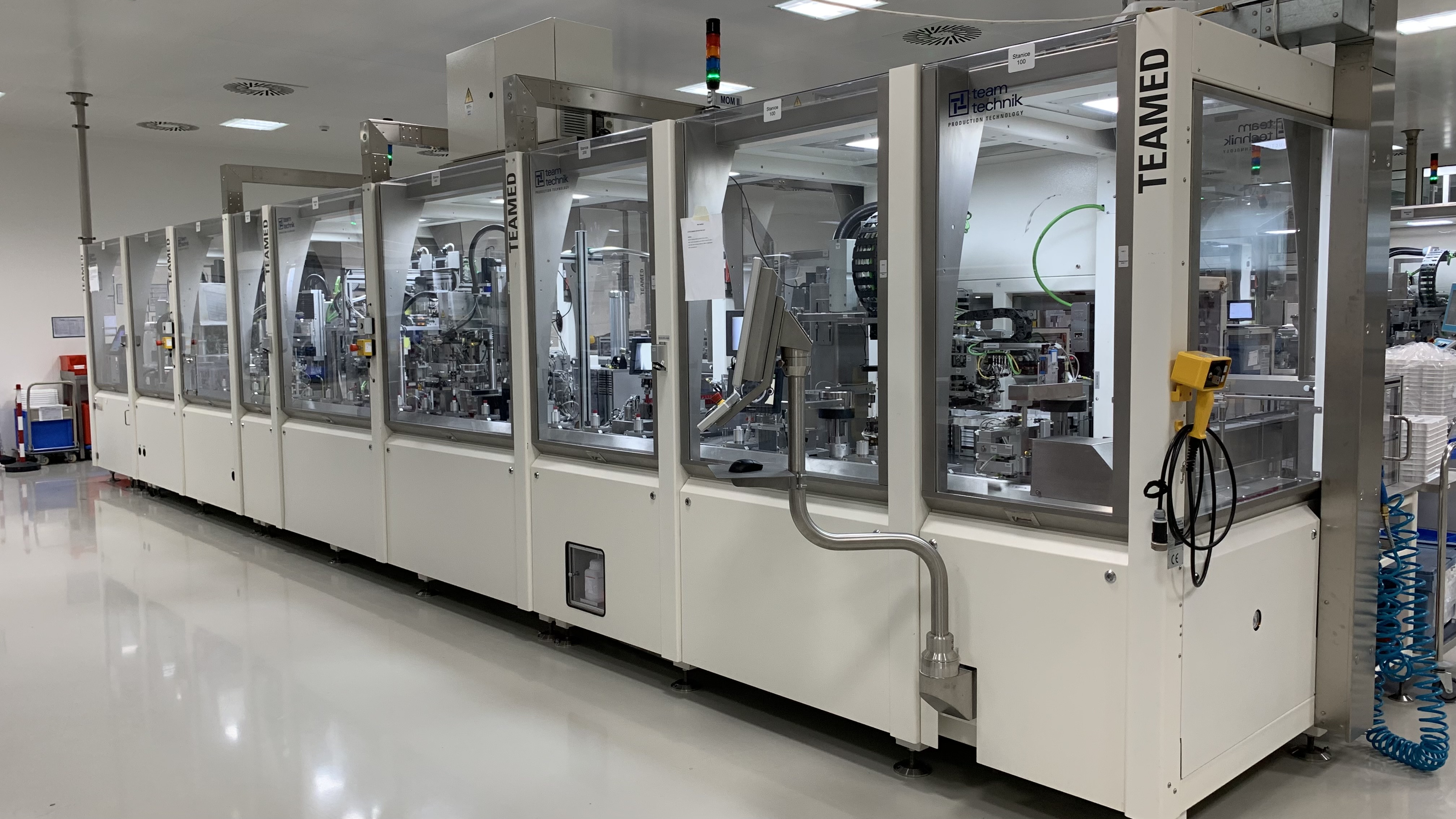